Advanced MPD delivers predictive ROP, optimizes drilling efficiency in Montney shale
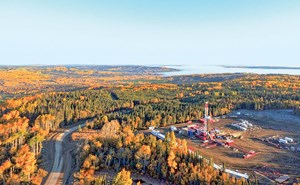
Applying automated managed pressure drilling (MPD) technology and distinctive drilling rate/mud density predictive modeling has enabled safe optimization of rate of penetration (ROP) in a three-well unconventional drilling program in Western Canada's largely over-pressured and naturally-fractured Montney formation.
Specifically, the capacity to manage differential pressures, and align advanced MPD technology with the predicted ROP, enabled the wells to be drilled trouble-free with low-weight, synthetic-based drilling fluid and with appreciably higher drilling rates. By comparison, offset wells drilled with conventional open-to-atmosphere circulation systems required a roughly 11.22 lb/gal mud weight, which effectively restrained average ROP to approximately 10.8 ft/hr. The automated MPD configuration drilled the competent shale intervals at a mud density of just under 8.0 lb/gal, yet averaged ROP of 24.2 ft/hr, with peak rates of 34.4 ft/hr.
Throughout the program, the advanced MPD system effectively held surface back pressure (SBP) in both static and dynamic conditions, to sustain a constant bottomhole equivalent circulating density (BHECD), which is especially critical in the Montney's abnormally pressured zones. Constant bottomhole pressure (BHP) was maintained for the entire operation in all three wells, which were drilled on the same pad, with various mud densities. The operation reduced drilling time by 13 days (conservatively) and reduced mud-related costs, while the lower density of the drilling fluid enhanced hole cleaning and minimized the risks of production-restricting formation damage.
Importantly, the automated MPD control system demonstrated near-instantaneous detection and control of unexpected gas influxes and circulated out a kick in 4 hr, thereby eliminating the need to shut in the well. Moreover, the project validated the intrinsic drilling efficiencies attainable when matching advanced MPD technologies with predictive ROP optimization simulations to maximize asset value.
THE MONTNEY PLAY
Generally described as an inter-bedded blend of low-permeability sandstone, siltstone and shale intervals, the Lower Triassic Montney formation traverses the provinces of British Columbia and western Alberta in the Western Canada Sedimentary basin. Typically, the Montney shales are 328 ft to 984 ft thick. They become thicker and more over-pressured with increasing proximity to the foothills of the Rocky Mountains, and they have abundant faulting and truncation in the western reaches of the play. The core of the play is extremely tight, is largely gas-saturated and has a profusion of over-pressured natural fractures.
Exploration of the prolific Montney shale began in the 1950s with vertical wellbores, but the play has since emerged as a highly prospective and extremely tight unconventional exploration target. Horizontal drilling in the Montney formation is characterized by high build rates and measured depths that often approach 18,000 ft. As in any tightly compacted and naturally fractured formation, drilling horizontal wells conventionally in the Montney shale has been extremely troublesome and notoriously slow, mainly because high mud weights are required to maintain well control in the fractured and over-pressured downhole environment.
Accordingly, an initiative was undertaken to adapt accepted ROP optimization theories to new-generation MPD technology to improve Montney drilling efficiencies. A key efficiency and economic driver for the engineering analysis was matching predicted ROP with lower mud weights.
ROP OPTIMIZATION METHODOLOGIES
Optimizing ROP—a key performance indicator (KPI) in any enhanced drilling efficiency model—is also one of the most difficult to achieve consistently. Maximizing drilling rates and, in turn, project economics, depends on myriad controlled and uncontrollable factors, ranging from permeability, porosity, compaction, compressibility and other rock characteristics to the bit type, nozzle sizes, weight-on-bit (WOB), mud motor specifications, and drilling fluid type and weight, among others. For the intended purpose of the Montney ROP optimization evaluation, the primary focus was on the mud type, properties, and density. Specifically, it was recognized early on, that by establishing pre-determined mud rheological parameters with respect to depth and using Neuron Networks methodology, any significant departure of the actual ROP from the predicted ROP trend could detect critical indications of ROP restrictors beforehand, and in real time.
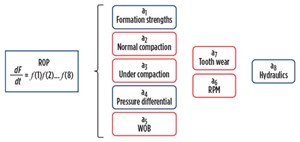
Following an evaluation of the three most commonly used ROP optimization models, the Bourgoyne and Young theory (widely considered the industry's most detailed mathematical drilling mode) was adopted as the baseline for the Montney project, because it is based on statistical synthesis of historical drilling parameters. For ROP optimization, detailed data analysis is critical for incorporating available data to modify the coefficients used in the proposed mode. Bourgoyne and Young provide a general, linear ROP equation that is a function of both the controllable and uncontrollable drilling parameters, expressed as:
(1)
The components of this equation are in Fig. 1.
Of the controllable and uncontrollable drilling parameters affecting ROP, this study considered only formation strength, pressure differential and hydraulics. Since the Montney wells were to be drilled on the same pad, the same coefficient for the effect of formation strength (a1) could be considered for all three wells.
As for the coefficient for pressure differential (a4), the Bourgoyne and Young theory holds that a pressure differential acting on the bottomhole will reduce ROP with decreasing pressure differences. Thus, if hydrostatic pressure, plus annular friction and wellhead pressure while drilling, is higher than the formation pore pressure, ROP should be reduced, compared to at-balance conditions, as expressed in equations 2, 3 and 4:
(2)
Thus, ROP declines when:
BHP = [HP=(MW×TVD×0.00981)+AFP+WHP] > PP (3)
Conversely, optimal ROP results when, BHP ≤ PP (4)
The effects of hydraulics (a8), though mostly related to bit jet hydraulics, also are directly affected by drilling fluid density, as indicated in equation 5:
(5)
Furthermore, in the ongoing quest to reduce drilling time, several researchers corroborated to demonstrate the influence of bit type, motor selection, weight-on-bit (WOB) and mud properties on bit hydraulics. Earlier work stressed the critical role of optimal bottomhole assembly (BHA) performance in maximizing ROP: A model proposed that an ideal WOB value can be estimated for a suitable motor to increase ROP in any interval, and with different lithologies.
Inarguably, however, the Dupriest and Remmert calculation of mechanical specific energy (MSE) remains among the widely used theories for destroying a given volume of rock to enhance drilling efficiency; it is defined as:
(6)
(7)
It has been proven in the field that using real-time analysis of MSE helps to achieve the most effective bit hydraulics, based on the WOB and the application-specific hydraulics specifications, namely torque and RPM. It was determined that certain factors could be changed to enhance bit hydraulics to reverse decreased ROP. On the other hand, when ROP is constrained by a factor outside of the driller's control, the MSE curve can be plotted, requiring the drilling engineer to remodel the drilling system.
In another practical approach, a comparison of different bit runs detailed the performance improvements arising from real-time parameter optimization efforts. By using an artificial neural network (ANN), engineering software could detect changes in drilling efficiencies, enabling the driller to manipulate the RPM and WOB to maximize ROP, while also minimizing bit wear rates.
ROP AND MUD SOLIDS
Striking a healthy balance between optimized ROP and effective hole cleaning was a critical consideration. It has been well-documented that drilling too fast can result in ineffectual solids removal and increased risk of nonproductive time (NPT) and unnecessary trips to deal with differential sticking, and excessive torque and drag. Conversely, although increasing WOB can speed up sluggish drilling, a number of drilling parameters must also be considered, when enhancing bit hydraulics to increase ROP. Among these is the concept that ROP is directly proportional to the mud weight (MW) and, in particular, its solids content, which is expressed as:
(8)
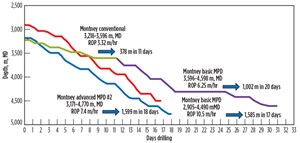
The increased density from higher solids concentrations in the drilling fluid elevates the pressure exerted by the fluid column on the wellbore. The increased pressure differential reduces ROP, and makes it more difficult to destroy rock and drill ahead. On average, the percentage of solids in conventional oil-based mud is 9%. It drops to 5% in brine and to a low of 1% in a synthetic-based mud (SBM). Based on equation 8, therefore, the drilling fluid with the lowest percent of solids will enable the highest ROP, thereby justifying the use of a low-density SBM for the Montney drilling projects.
OPTIMIZED MONTNEY ROP
As mentioned, a single operator drilled the three wells on the same pad, targeting the Montney formation, Fig. 2. The first well was drilled conventionally to just under 11,798 ft, MD, at which point drilling began in the basic MPD mode, using a manual choke. Results of drilling the other two wells with the advanced automated MPD equipment and control system are indicated by the red and blue lines. For the automated MPD technology, the system’s annular pressure control mode was used to hold a desired ECD at a predetermined position within the wellbore, which in this case was the heel. Constant BHP was maintained throughout the project with the desired ECD—often referred to as the equivalent mud weight (EMW)—sustained at balance with the pore pressure.
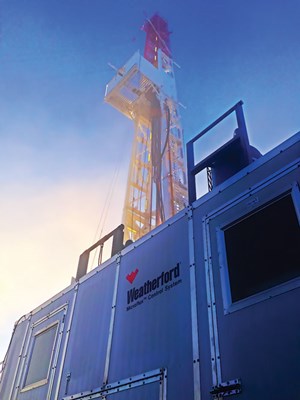
The conventional drilling system required 31 days to drill 4,278 ft of hole, but the advanced MPD system safely drilled 5,200 ft and 5,246 ft of the lower intervals of the two Montney wells in 17 days and 18 days, respectively, Fig. 3. The ROP of the conventionally drilled section averaged just under 11 ft/hr, but nearly doubled to more than 20.5 ft/hr when drilling commenced with the basic MPD manual choke system. In the remaining two wells, the automated MPD technology drilled at an average ROP of more than 24.2 ft/hr and 34.4 ft/hr, respectively. Compared to the conventional drilling rate, the basic MPD intervals were drilled at 188% higher efficiency, while the two advanced MPD wells achieved 316% and 223% increases in comparable efficiencies.
Furthermore, the wells drilled with the advanced MPD systems not only reached TD nearly two weeks faster than the conventional well, but also drilled deeper horizons, further reducing well construction costs.
REDUCED MUD WEIGHTS
A widely recognized advantage of advanced MPD technology is the ability to drill safely, with lower mud density and near-instantaneous application of surface backpressure, to automatically increase EMW to control unexpected influxes and pressure spikes. The SBP component of the advanced MPD technology, which enables real-time control and manipulation of the BHP, enabled faster drilling with lower-weight muds that were formulated with fewer and less costly products, compared to their higher-density counterparts.
The aforementioned pressure differential (f4) and hydraulics (f8) factors both depend on a given MW as a critical factor within their respective mathematical models. Therefore, based on the Bourgoyne and Young theory, decreasing the MW will increase ROP in each case, as explained by:
Differential pressure:
(2)
ROP is low when:
BHP=[HP(MWxTVDx0.00981)+AFP] > PP (3)
Thus, reducing MW also reduces the overbalance effect and optimizes ROP hydraulics:
(5)
Here, the reduction of MW (ρ), which reduces the effect of bit hydraulics, in conjunction with pressure differentials, optimizes ROP.
With respect to both differential pressure and hydraulics, using MPD can logically optimize ROP by reducing and stabilizing the BHP within a safe pore pressure margin, thereby enabling the MW to be lowered to the closest acceptable value.
For the Montney wells, simulations were conducted using varying mud weights. Post-well analysis showed extremely close correlation between the actual MW and those predicted in the model. Thus, actual fluid densities were safely reduced from a high of 11.3 lb/gal to a low of 7.9 lb/gal.
MONTNEY ROP PREDICTIVE MODEL
For the Montney wells, prediction of the change in ROP that results from adjusting the MW for a given formation was provided by Bourgoyne and Young, whereas:
(9)
Using offset well data from the Montney and rearranging the equation, the critical formation factor (FF) can be calculated with:
(10)
Ostensibly, to accurately estimate the FF, one should use at least two different mud densities, at the same depth from two or more offset wells. In addition, the corresponding ROP is needed for the given depth and MW. Once the FF is calculated, it is re-inputted into equation 9, thereby allowing repetition of the iterative process until a suitable degree of accuracy is achieved. The calculated FF values at each depth are averaged. Since the Montney wells were all drilled from a single pad, it was only necessary to determine the FF for the first well and then to use the same value for the other two wells.
Equations 9 and 10 were applied to offset wells drilled conventionally in the Montney with measured depths ranging from 10,006 ft to 11,785 ft, and MW varying from 10.7 lb/gal to 13.1 lb/gal. The Montney formation was then subdivided incrementally, and the FF was calculated for each increment, providing an optimal, calculated FF value equal to 1.44 x 10-5, which was applied to all three wells.
Data analysis of the Montney wells showed ROP typically decreased from 10,171 ft to 10,955 ft, MD, even though an analysis of offset bit hydraulics showed torque, WOB and RPM all remaining constant. The only reasonable conclusion was that lithological changes in the Montney, at that depth range, slowed drilling rates.
The predicted well results derived from Equation 9 with the constant FF of 1.44 x 10-5 clearly demonstrated that the 10,007-to-11,785-ft, MD, interval programmed for the advanced MPD system could be drilled safely with a 7.0 lb/gal SBM mud. The prediction tool determined that the lower MW would improve the drilling rates from 10.7 ft/hr to 18.3 ft/hr, all the while maintaining constant BHP by closing the choke on surface and applying SBP.
Comparing results from the basic MPD and the automated MPD systems in their respective intervals shows the former averaging 18.2 ft/hr at a corresponding 8.5 lb/gal mud weight. For the advanced MPD sections, the MW was dropped to 7.7 lb/gal, and average ROP increased to 18.2 ft/hr.
MODEL PERCENTAGE ERROR
The accuracy of the model and FF was verified by comparing the predicted ROP to the actual drilling rates. Actual field data on the second well showed that the advanced MPD technology drilled with an average ROP of 24.2 ft/hr, while the median ROP of the basic manual choke MPD system was at 20.5 ft/hr. By far, the conventionally drilled sections were the slowest, at an average ROP of 10.8 ft/hr.
The percentage of error in the model was calculated as:
(11)
An analysis of the MPD sections of these wells revealed a model-high percentage of error, when comparing actual ROP to a numerical value within the predicted range of ROP. This reinforces how the lack of sufficient offset data prevents fine-tuning the formation factor, when using an iterative approach to solve the Bourgoyne and Young equation. However, for this program, the model served to further validate the inherent benefits of using MPD technology in concert with the Bourgoyne and Young theory, to optimize ROP, and to evaluate conventionally drilled offsets to fully understand the formation factor within the competent Montney formation.
- Applying ultra-deep LWD resistivity technology successfully in a SAGD operation (May 2019)
- Adoption of wireless intelligent completions advances (May 2019)
- Majors double down as takeaway crunch eases (April 2019)
- What’s new in well logging and formation evaluation (April 2019)
- Qualification of a 20,000-psi subsea BOP: A collaborative approach (February 2019)
- ConocoPhillips’ Greg Leveille sees rapid trajectory of technical advancement continuing (February 2019)