NOV's Tektonic drill bits increase ROP, durability with Permian Series cutters
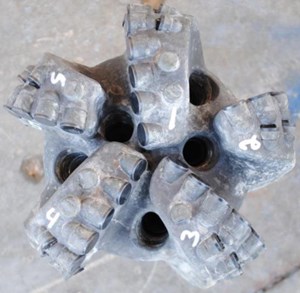
HOUSTON -- Difficult drilling conditions in the Permian basin demand a drill-bit philosophy geared toward efficiency and durability. ReedHycalog, a business unit of National Oilwell Varco’s Wellbore Technologies segment, developed Tektonic drill bits with Permian Series cutters to address the challenges of operators in the region and drive improvements in ROP.
The drill bits are designed to initiate rock failure efficiently to achieve maximum ROP. A low-friction cutting surface enables cuttings to move up the front face of the cutters and along the front of the blade more efficiently, and improved blade geometry optimizes downhole loading. Blade height and root geometry are customized to each operation, enabling increased drilling performance, improved cuttings evacuation, and better cleaning and cooling. This is made possible by efficient hydraulic design utilizing computational fluid dynamics.
Permian Series PDC cutters, when run with the Tektonic drill bit, allow operators to overcome critical failure modes in the challenging interbedded formations typically seen in complex Permian wells. As durability was a major design factor for the cutters, the new version incorporates refined diamond feeds and uses increased sintering pressures to resist both impact damage and abrasion while maintaining thermal stability. Permian Series cutters have a more effective cutting edge that increases ROP without sacrificing durability, and cutter geometry has been optimized using both modeled FEA and extensive field testing to reduce drilling torque and MSE. Permian Series shaped cutters can further increase efficiency and performance.
Three record runs recently occurred in the Permian basin that showcased the performance of the bits with Permian Series cutters. On the first, an operator needed to drill a long vertical, from 985 to 8,768 ft, at a higher speed than previously achieved in benchmark wells. Incorporating the new 8¾-in. TK76-F bit design, the operator drilled the entire vertical in 40.8 hr, reaching an average ROP of 190.8 ft/hr. This was the fastest drill-out run achieved by the operator in Lea County, New Mexico for a vertical of more than 7,000 ft, and the bit drilled 16.3% faster than the previous top four runs in the same interval.
On the second run, an operator in Ward County, Texas needed to drill a difficult curve section with a single bit without exceeding 11 hr of on-bottom drilling time. Using an 8¾-in. TK56 bit design, the operator drilled 200 ft of vertical before building up to the 890-ft curve. The curve was drilled in just under 11 hr at an average ROP of 70.3 ft/hr, surpassing the operator’s expectations for ROP and achieving a top-five curve run, using ReedHycalog bits, by the operator in the region. Additionally, the bit finished the section with an excellent dull condition of 0-2-CT-G-X-I-BT-TD, indicating the durability of the Permian Cutters when drilling in the section’s complicated lithology, which consisted of both shale and sandstone.
On the third run, an operator in Reeves County, Texas needed to drill an extended lateral in one run. The formation consisted mostly of shale with interbedded limestone, with some layers of sandstone also present. To address these lithological complexities, the operator chose the ReedHycalog 6-in. TKC56 with Permian Series shaped cutters. The operator drilled the 9,910-ft lateral for 141.4 hr at an average ROP of 70.1 ft/hr before reaching TD. This was not only the longest lateral run with a 6-in. ReedHycalog bit in Reeves County, but also the furthest versus a competitor—form landing point to TD, the bit outperformed the closest design by 4,115 ft.