Drilling technology: New ML-based drilling system recommender app demonstrates AI’s inherent value to well construction
Imagine this: You are a drilling engineer planning an upcoming well or hole section. You may have experience drilling similar wells near the planned well, or maybe this is an exploration well in a completely new area. Maybe the well is offshore and extensively planned over months. Or, maybe it is part of a factory drilling campaign in the U.S., where new wells are batch-drilled in days and a new drillstring is picked up once or more per day, leaving little time to analyze data.
Regardless of the situation, your goal is to drill within an expected budget and timeline while meeting other wellbore objectives, such as adhering to the designed trajectory and maintaining a certain wellbore quality. You must design the drilling system, including the drilling fluid, bottomhole assembly (BHA), motor, and drill bit, to deliver the best drilling performance for each interval, or hole section, of the well.
Decisions made by engineers significantly impact drilling performance. Among key decisions they must make is which components to select for the drilling system, including which individual component selections are well-suited for the entire system. For example, the drilling fluid must satisfy all requirements for hole cleaning and wellbore stability. It also must be compatible with internal components of the BHA.
DATA CHALLENGE
Today’s engineers have access to vast amounts of data and information accumulated from global operational experience. Some factors that are commonly considered include local offset well analysis, prior experience, physical modeling, tool availability and cost, and consultant advice from service companies. It wasn’t always this way. Traditionally, tough drilling decisions were made by counting on the engineers’ collective memory of how similar situations had been managed in the past. Today, the challenge isn’t about having enough data, but about being able to use it to its fullest potential. The desire is to extract details from previous runs that will enable faster and more intelligent decision-making for selecting the best combination of equipment to optimize performance in new runs. Digital transformation is addressing this challenge.
Currently, real-time (RT) data streams, advanced process models, and sophisticated simulation techniques are used to monitor well construction operations. But decision-making is still primarily performed by humans, with little automation. Decisions are based, not only on interpretations of the model outputs, but also to a large extent on past experiences, and sometimes on “gut feelings.” It has become abundantly clear that a high-level, data-driven workflow is necessary to assist the decision-making process.
AI/ML SOLUTION
A new data-driven, machine learning (ML)-based drilling system recommender (DSR) developed by SLB and deployed to a global group of drilling engineers employs such a workflow. The DSR uses historical drilling performance data and key performance indicators (KPI) to provide previous drilling system technology selection choices and results to today’s drilling engineers, to help them optimize equipment selection decisions for upcoming well sections during the planning phase.
Bringing AI and ML to well construction. Artificial intelligence (AI) describes the ability of computers to be trained to recognize patterns, classify images, and anticipate behavior by analyzing vast streams of data. One of the main objectives of AI is to solve complex problems by applying the ability of machines to gain knowledge, or learn, from large chunks of data and use these “lessons” to either predict the outcome in a certain environment or suggest the environmental boundaries most likely to lead to certain outcomes. This capability of computers to gain knowledge from experience defines machine learning (ML), which is considered the most successful aspect of AI.
While the human brain may be able to guess the impact of tweaking one or two variables, an ML model can do the same with hundreds in a fraction of the time. Herein lies the inherent value of AI and ML in decision-making, including for well construction. As data science and ML applications become easier to access and use, they are setting the stage for rapid scaling across the E&P industry to assist the human decision-making process.
Recommender (or recommendation) systems form a popular class of ML tools that are implemented in many consumer applications to change the decision-making process. As the engines behind these systems are becoming smarter by using various statistical and ML approaches, they are now further optimizing drilling operations.
The team that developed the DSR recognized the industry goals to reduce operation time and increase consistency and realized that providing historical equipment selection and performance results through an intuitive user interface could help achieve these goals. Where the DSR diverges from consumer-type digital recommendation systems is that while the latter rely primarily on user preferences, the DSR relies on historical performance and other KPIs that are important within the context of the decision to be made.
The KPI concept allows the recommendations to be based on what is ultimately important to the user—i.e., performance or reliability. For example, is it the average rate of penetration (ROP) of the run, the success rate of similar runs drilled with a certain tool, or the cost of the specific tool? The importance of each KPI can be fine-tuned, using the KPI importance weights, which the users can modify based on their preferences and changing needs.
The database: the power behind the DSR app. Ultimately, the usefulness of digital recommenders comes from the data on which the engine is built. The developers of the DSR realized early on that historical drilling system design decisions and operational outcome data were stored in multiple legacy well construction databases within the company. Thus, an extensive effort was made to bring these data together and structure it in a systematic way for ease of consumption.
The DSR development relied heavily on collecting, organizing and standardizing data from these databases. They included a legacy bits and tools database, a legacy directional drilling service database, and a legacy drilling fluid database, all based on hundreds of thousands of wells drilled worldwide. The consumption database is refreshed daily with new operational data and is made available to internal data science and data analytics workflows, Table 1.
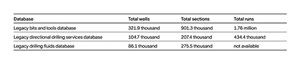
All these data are hosted on a cloud environment, ensuring that access is controlled, using the minimum access concept, and conforming to strict data residency and data rights-of-use rules. Making the data available on the cloud opens the door to using current best practices for developing and deploying data science applications to a global user base. To standardize the data, a common table plan was established. Additionally, an extensive data engineering pipeline was developed to transform the data into a set of tables, which are usable from data scientists to business users. This new database powers the DSR app.
How the DSR app works. The end-user of the DSR web app is a drilling engineer, who is planning an upcoming well. The web app has multiple pages—one page for each decision to be made. These decisions are typically made in a predetermined order, e.g., the drilling fluid is selected, followed by the BHA, then the motor power section, and finally, the PDC drill bit. For each decision, the user is required to enter the parameters of the planned run, which are essential for the decision to be made. After inputting the required data, the recommendations are displayed, and additional analyses can be performed by modifying the input data, changing the KPI importance weights, or simply analyzing the various data visualizations, Fig. 1.
After the drilling engineer defines the parameters of the planned drilling run, the DSR app automatically selects the most similar previous drilling runs within the context of the technology selection. Once the most similar offset runs are determined, the technology selection decisions are scored for numerous KPIs. These and user-defined KPI importance weights drive the overall scores. The drilling engineer can also fine-tune the offset selection, based on experience using filters in the app. Finally, technology selection recommendations are made, based on the overall scores and other contextual data, such as local availability and cost.
The web app has been deployed to a global group of drilling engineers. For each recommender page, feedback sessions are held regularly, and the development team uses this feedback to rapidly iterate and improve user experience. Throughout this process, countless improvements have been made to the web app, to the engines, and even to the underlying database and data engineering pipeline. We believe that this feedback from actual users is essential to the success of the developed application.
Drilling fluid recommender. The drilling fluid is an essential technology in the well construction process. As complex chemical systems, drilling fluids also have numerous and often contradictory requirements, which makes the proper choice challenging. Recent efforts to profile drilling fluids in a variety of properties to understand similarities and differences in their performance and cost led to the concept of the drilling fluid recommender.
The drilling fluid is recommended for the planned well interval. Drilling fluid KPIs include drilling ROP, time used on various remedial activities (hole conditioning, stuck pipe, etc.), fluid treatment frequency, additives cost, and fluid complexity. All the fluids used in the offset intervals are ranked for each of these performance characteristics. Depending on local requirements or constraints and other considerations, the user is empowered to weight performance metrics differently to find an optimal fluid system. While drilling fluids are recommended for the planned well interval, the remainder of the recommendations are for the planned drilling run.
BHA recommender. A drilling system’s BHA typically consists of various downhole tools, including measurement-while-drilling (MWD) and/or logging-while-drilling (LWD) tools. However, the primary objective of the BHA is to steer the drillstring along the well’s planned trajectory. Hence, the BHA commonly contains a steerable tool, such as a positive displacement motor (PDM) and/or a rotary steerable system (RSS). BHAs can be classified according to which steerable tool(s) are used—non-steerable BHAs, steerable motor BHAs, RSS BHAs, and motorized RSS BHAs.
The objective of the BHA recommender is to advise on the best combination of BHA type and RSS model for the planned run. Once the most similar offset runs are identified, they are used to determine which BHA types and RSS models were used, as well as a statistical view of how each combination performed. BHA KPIs include ROP, drilled footage, maximum dogleg severity achieved, run success rate and number of runs. An overall score is computed, based on these five KPIs and their individual KPI importance weights, which can be modified by the user.
Motor power section recommender. After the BHA type is selected, additional tool selections can be made. If the BHA will use a PDM, the motor power section configuration (PSC) must be selected. Thus, the objective of the motor power section recommender is to advise on the best motor PSC. The PSC is defined as the motor diameter, lobe configuration, and number of stages—the same way PSCs are represented in motor handbooks and catalogs.
Motor PSC KPIs include drilling ROP, drilled footage, run success rate, downhole motor failure rate, and number of runs. As with the other recommenders, an overall score is computed, based on the five KPIs and their individual KPI importance weights, which can be modified by the user. The motor PSC web app user interface (UI) is shown in Table 2.
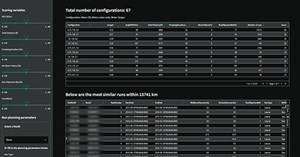
Drill bit recommender. Once the drilling fluid, BHA, and motor have been selected, a drill bit must be selected that is not only compatible with, but also complements and maximizes the performance of the overall drilling system. However, drill bit designs are extremely numerous. Polycrystalline diamond compact (PDC) bit designs are increasing in numbers, due to the explosion in shaped diamond element technology. Various types of shaped diamond element PDC bits are yielding enhanced drilling performance in some applications but are also making the task of selecting a drill bit design significantly more complex. Not only are there numerous drill bit designs, but new designs are frequently released. This situation presents another challenge, because newly released bit designs have limited or no actual field performance data on which to base the KPIs used by a drill bit recommender engine.
For these reasons, the objective of the drill bit recommender engine is to predict the following four key PDC bit design features, rather than a specific drill bit:
- Number of blades
- Cutter diameter
- Shaped diamond element technology (or PDC if no shaped cutter technology is used)
- Bit body material type (either matrix or steel).
Based on the predicted bit design features, a search engine is used to find all PDC bit designs that match the predicted design feature set. The KPIs are then computed for each bit design when field performance data are available. When these data are not available, which is possible for newly introduced bit designs, the bit designs are still displayed, because the user might want to consider them in some way—for example, include them in a physical modeling study.
The interface of the web app is shown in Fig. 2. User inputs, including the planned run parameters, the KPI importance weights, and optional bit design feature filters are provided on the sidebar, on the left side of the screen. The recommended bit designs, including images of the top three, and a complete data table listing all recommendations, computed KPIs, and overall scores, are provided on the main section of the screen. The KPIs include drilling ROP, drilled footage, run success rate, and bit severe damage rate (a severely damaged bit often incurs a financial penalty fee to the operator).
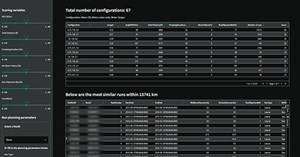
VALUE DELIVERED
A new DSR has been developed to assist drilling engineers in selecting the drilling fluid, the BHA, the motor power section, and the PDC drill bit design during the well planning phase. These recommenders use ML algorithms to learn from global offset well data in finding the most similar drilling runs, or directly predict features of the drilling tools. A statistical approach is then used to score the selection options and rank them in terms of performance and the user’s context, of which KPIs are most important for their decision.
While drilling engineers have access to a vast amount of data and information, these items often cannot be used in a practical and efficient way. The new solution places all the previous drilling system technology selection choices and results into the hands of the drilling engineers, to empower them to make their best decisions. This effort shows how ML and innovative software deployment methods can, in fact, assist the human decision-making process and succeed in the goals of digital transformation. Proper drilling system selection is critical to achieve industry-wide goals of reduced operation time and increased consistency.
Path forward. SLB is working to deploy the new DSR technology directly to operators, based upon their own internal drilling performance databases. This allows the operators to improve their decision-making, based upon data they trust most. Future goals of the ML-based DSR are joint, and ultimately, holistic system recommendations. Research efforts continue toward meeting those goals. Incorporating more data will improve the model’s performance in making more accurate recommendations. The expectation is for the machine learning model to reduce drilling downtime, improve efficiency and performance, and ultimately reduce development cost for the operator.
ACKNOWLEDGEMENTS
This article contains excerpts from two technical papers, including “Machine learning-based drilling system recommender: Towards optimal BHA and fluid technology selection,” SPE paper 212559-MS, presented at the SPE/IADC International Drilling Conference, Stavanger, Norway, March 7-9, 2023. And “Machine learning model for drilling equipment recommender system for improved decision-making and optimum performance,” SPE paper 211731-MS, presented at ADIPEC, Abu Dhabi, UAE, Oct. 31 – Nov. 3, 2022.
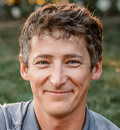
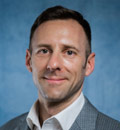
- Accessing wells beneath deepwater facilities (December 2024)
- Sustainability: Meeting new drilling demands with smarter power management (November 2024)
- Digital control architecture optimizes plunger lift wells (November 2024)
- Cognite: “Un-siloing” data with generative A.I. (November 2024)
- Automated intelligent chemical injection technology minimizes corrosion/scaling, extends ESP run life, increases Permian production (November 2024)
- U.S. footage drilled per well continues to creep higher (October 2024)