Accessing wells beneath deepwater facilities
Interview with Nathan Wolford and Kevin Knight, C-Innovation, USA
Subsea operators have long been limited in the options they have to stimulate subsea wells within a drill center while a mobile offshore drilling unit (MODU) or production facility is moored overhead. Tieback wells have the advantage of being far enough away from the facility to allow an intervention vessel to arrive onsite without a major disruption of production and drilling operations, but the wells “under the shadow” of the facility require a rig move (via mooring adjustments) and platform-based, direct vertical access intervention riser systems—equating to extensive deferred production of many wells to improve production of a single well.
C-Innovation (C-I) has become an intervention market leader in the Gulf of Mexico by offering turnkey, vessel-based, riserless light well intervention services. Accordingly, the firm has devised a novel hydraulic intervention methodology to access wells that are normally inaccessible by intervention vessels, due to topside obstructions, by operating from an offset position. World Oil recently had a conversation with Nathan Wolford and Kevin Knight of C-Innovation, USA, to learn more about this new riserless well stimulation solution, which keeps facility and vessel from being too close for comfort.
World Oil (WO): How does the industry typically approach a hydraulic well intervention—a.k.a., a subsea well stimulation?
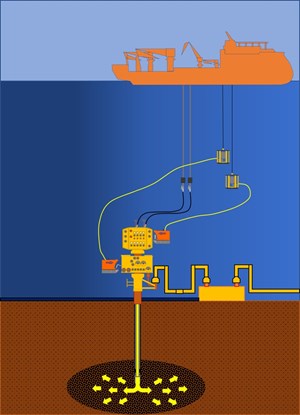
Kevin Knight: Offshore production facilities are designed and built to perform a fixed set of activities within the confines of a fixed area. For deepwater developments, this location can be hundreds of miles offshore. Some of the major operators’ larger facilities are equipped with the ability to deploy a riser-based intervention system to gain direct vertical access (DVA) of a wellbore through the subsea tree (XT). Nowadays, DVA can be considered overkill when performing a hydraulic intervention. If you have a completion & workover riser (CWOR) system aboard the platform, facility repositioning is necessary to gain DVA. If you want to inject the stimulation chemicals into the subsea production system (i.e., riser, flowline, manifold, jumper), that could create system lifespan concerns.
Whereas the production systems are specified and designed to contain the produced hydrocarbons (and subsea-injected, flow assurance chemicals), a common well stimulation will flow caustic acids and other treatment chemicals through the system into the reservoir. The production system materials may not have been chosen to anticipate exposure to these chemicals, and (in an intervention) they will have to pass through the system twice—i.e., once to pump into the reservoir for stimulation, and again to flow out of the well to restart production.
Flow path aside, the platform must play host to necessary intervention equipment. Many times, platforms simply do not have the space nor the equipment to accommodate this; and, even if a stimulation vessel can be brought alongside the facility to supply the stimulation fluids and high-pressure pumping capability, a relatively large footprint still needs to be identified and cleared for the additional, temporary process equipment necessary on the platform.
Nathan Wolford (NW): This all comes at great cost and impact to production operations. On shared facilities, smaller operators wanting to carry out this work might even be prevented by the larger operator, who does not want to sacrifice space on the production facility and have their operations impacted. If a hydraulic intervention continues to be delayed, that well’s production will be impacted to the point where the ability to produce is lost altogether. There are also other costs associated with deferred production. Oil may be priced around $100/bbl today, but it may be half that value in six months’ time, so it pays to have the ability to produce when prices are favorable. Our goal is to offer operators solutions that allow them to plan and execute timely well interventions according to need. Timing is everything.
WO: What is C-I’s standard approach to well intervention? (Fig. 1)
Wolford: C-Innovation, in partnership with our alliance companies, offers turnkey, vessel-based, riserless light well intervention services to our clients—encompassing the entire well intervention system. This includes provision of the vessel, ROVs, subsea intervention/well control system, pumping system, coiled tubing (for fluid conveyance), nitrogen, and stimulation fluids. We typically land a well control package (WCP) on top of the subsea tree to gain access to and establish new barriers for the well. Stimulation fluids are injected through the open-water coiled tubing downlines connected to the WCP. The operations are safe and efficient and not subject to the availability of slow-moving drilling rigs with CWOR systems—traditionally used for this type of scope. C-I has established a track record of performance on 69 riserless well interventions using our vessels Island Venture, Island Intervention and Island Performer.
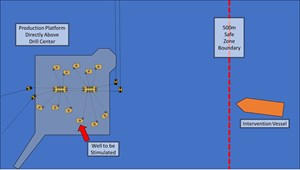
WO: What particular challenge led to rethinking this approach? (Fig. 2)
Wolford: Many facilities do not want operations occurring within 500 m of the facility for safety reasons, and rightly so. The controlled deployment (and recovery) of equipment to deepwater, subsea oilfields is subject to the movement of the ocean, and if control of the equipment is not maintained and collisions occur, hydrocarbon release to the environment is a possibility, and personnel safety may be at risk. The challenge, therefore, was to not get too close to the production facility with the intervention vessel. We had to design a system that limited our time of exposure to a relatively small window, when sea conditions were ideal. C-I developed a new well intervention system that enables operators to reach under the facility and access those wells to perform hydraulic interventions, while minimizing impact to production facility operations.
WO: What was your solution to this problem? (Fig. 3)
Knight: We adapted our hydraulic intervention solution to operate from an offset position with a system expansion we call the “Well Service Jumper.” This concept moves the WCP—in this case, we use a manifold known as a Riserless Stimulation Tool (RST)—off the tree and onto a mud mat, which is placed in an approved location on the seabed outside of the shadow of the platform. This installation location is relatively close to the facility (but not directly underneath it), and the intervention vessel uses good sea states and its crane reach capability to ensure it maintains a position outside of the mandated minimum separation distances between the facility and the vessel.
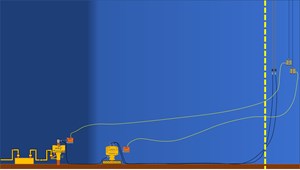
Then, high-pressure hose jumpers are used to connect the RST to XT and the injection pumping system to the RST. It’s like using long electrical extension cords during a power outage to connect lamps and appliances inside your house to a gas-powered generator outside of your house. The distances covered by the lay path of the hoses allow the intervention vessel to operate from a position farther away from the production facility, effectively expanding the window of safe operating conditions (i.e., weather and sea states). The nimbleness of vessel-based operations further promotes uninterrupted operations through dynamic positioning (automated propulsion adjustments for station-keeping during increased sea states) and weathervaning (heading adjustments in relation to a chosen pivot point) capabilities.
Wolford: The well service jumper system was deployed to a high-producing subsea development for a major operator in the Gulf of Mexico. The wells were vertical completions located in approximately 6,000 ft of water below a moored drilling and production facility. All necessary intervention equipment and materials are brought out on a vessel, meaning the production facility can still be actively engaged in other planned operations that require specific positioning or direct vertical access to a well installed below it. The only impacts to the facility are those directly associated with the intervention activity—e.g., taking the well offline, deferred production, flowback processing, etc.
WO: What are the main components of the system?
Knight: The system comprises the Well Service Jumper, RST, and Hybrid Catenary Flexible Downlines. The Well Service Jumper is a single-hose assembly that can be built up to 750 ft in length to connect the output of the RST to the input of the XT. The importance of this system component cannot be understated; it extends the reach of the intervention system to underneath the production facility, so it must be able to be guided into place by remotely operated vehicles (ROVs) using their available tethers to make these long excursions.
The RST is a subsea manifold deployed via crane that is designed to provide well control barriers and high-flow fluid injection capability. The base configuration of the RST is to land atop a vertical subsea tree (XT) with fluid discharge out of the bottom connection and directly into the XT. However, for this application, it is fitted with a bottom adapter spool for side outlet and mounted on a mud mat for placement on the seabed. Consequently, this also allow access to a horizontal XT via a choke insert.
Wolford: The manifold provides high-flow hydraulic access to the well with two 2-in. downlines (for fluid conveyance from the intervention vessel), along with well control capability. In the event of an emergency, the valves can be closed quickly to contain the well and protect both the environment and the intervention crew. A further modification was made, whereby instead of everything discharging out of the bottom of it when clamped onto an XT, another pipe spool underneath allowed for a side outlet. This allowed it to mount on a mud mat and be located outside of the shadow of the facility.
Our fluid downlines provide us with the greatest amount of offset distance between the intervention vessel and the production facility. This arrangement starts with two spools of coiled tubing (CT) deployed from the vessel deck directly through the water column. It is noteworthy to mention that this open-water deployment of CT strings—i.e., without the additional containment of rigid marine riser pipe for “pipe-in-pipe” deployment—is what technically qualifies our hydraulic intervention solution as “riserless.”
Within 100 ft of the seabed, each CT string is transitioned to the same high-pressure hose used for the WSJ except, in this case, the lengths are up to 1,050 ft to create temporary intervention flowlines along a chosen path on the seabed between the RST’s installed location and the intervention vessel’s approved operating location. A dual-containment weak-link connector is installed between the CT and flexible hose to allow for separation of the downlines in the rare event that the vessel must make an emergency break-away from the subsea portion of the system.
WO: If the intervention manifold is no longer on the XT, how did you gain access to the well?
Wolford: Placing the manifold was relatively straightforward. On the production facility, no subsea crane was available, and there was a desire not to interfere with facility operations. The MSV crane had no vertical access to the well. A modified strategy was, therefore, required.
Knight: To obtain hydraulic access into the well, a modified XT cap (for vertical XT applications), which was light enough for ROV installation (with the help of buoyancy), was deployed from an MSV outside the facility footprint. It was then flown by the ROV to the XT, with minimal facility impact. The most straightforward access method is through the top with an intervention package, then choke replacement, if equipped. Finally, pumping through a manifold slot has huge impacts on the production of the drill center. Every XT has a removeable XT cap, which serves as a barrier between the wellbore and the ocean, so that was the chosen access.
The swab valve serves as the XT’s primary barrier to the environment when producing. It is manually operated via ROV and remains closed. Before the XT cap is removed, the master- and wing valves are closed and verified as primary barriers. C-I ensured that the swab valve was closed and holding properly and then took out the XT cap and replaced it with a modified design that provided high-flow hotstab access via the well service jumper—i.e., a 2-in. internal diameter hose assembly that connects the XT to the WCP. Once this connection is installed and tested, the required primary and secondary barriers for the well move from the XT to the RST.
Because our initial base case was for vertical XT applications, we were able to modify a tree cap to include a high-flow hotstab manifold for fluid injection. Every VXT has a removeable tree cap that serves as one of two verified barriers between the wellbore and the ocean—the other being the ROV-operated Production Swab Valve. By closing the Production Master Valve to establish another barrier, we could confidently swap out the regular tree cap for our Intervention Tree Cap. Once the well service jumper is connected, and the RST barrier valves are verified via required subsea testing, the PSV and PMV can be locked open for the duration of the intervention—allowing uninhibited fluid injection access to the well.
WO: That only gets you out from under the facility—how did you get the vessel farther away?
Knight: This is where the previously mentioned 1,050-ft flexible jumper assemblies are key. We used these long hose assemblies to span the distance along the seabed between the RST’s installed subsea location and the base of the water column directly below the vessel’s designated operating location.
Wolford: Since 1,000 ft of hose is both expensive and difficult to handle, we chose segmented hose for the ease of replacing individual damaged segments instead of needing to send off the whole hose for repair. This proved to be a very beneficial decision.
Knight: For deployment, the downlines are payed-out from spools on the intervention vessel, and the boat determines the lay path with its maneuvering to the operating location. The ROVs monitor this laying process to ensure the path is without obstruction or risk of damage. Since we’re deploying in water depths upwards of 6,000 ft, the hanging weight of the hose assemblies was the primary factor limiting the final length that we could deploy in any one string. Fortunately, the nominal 1,000 ft allowed us to reposition the vessel into the 300-m zone (from the facility); this does not achieve the ideal 500-m zone, but it still offers a manageable window of operational limitations.
WO: Why didn’t you avoid the difficult handling of all that hose and just lay coiled tubing on the seafloor?
Knight: The short answer is flexibility. Firstly, coiled tubing is metal pipe, and vessel motion—due to sea states—would increase the fatigue on the pipe in the area where it interacts with the seabed, transitioning from a vertical to horizontal configuration (a.k.a., touchdown point, or TDP). Of course, with enough cyclic stress, even armored and jacketed high-pressure flexible hose will eventually fatigue to the point of yield, but this takes substantially more effort, due to the smaller minimum bend radius and construction materials. Secondly, if a hose did manage to fail, we can remove and replace that 150- ft segment in the affected downline.
WO: What if the weather changes—are you able to get away with all that hose?
Wolford: That is a valid concern, because these stimulation jobs can require days of non-stop pumping and, as we’ve seen, the Gulf of Mexico can be rather active with respect to weather. The short answer is, “No, but we don’t have to.” Our operations team constantly monitors the weather and we can recover the downlines with enough advance warning. In the event we cannot recover, due to a fast-moving system or a sudden squall, we can adjust the vessel position and/or the CT deployed length to better handle the elevated seas. As a last resort, if conditions deteriorate quickly and severely, we have installed mid-line weak-links in the downlines, which will separate, if they are placed in high-enough tension. These devices provide full containment of the contents with minimal (if any) fluid loss.
WO: It sounds like a lot of effort to install the system. Do you have to recover and re-deploy for every well stimulation job?
Knight: No, if the client plans to stimulate multiple wells in a single drill center, we can plan the system installation to allow for infield manipulation of the WSJ, then the ROVs can simply unplug from one well, adjust the lay pattern, and plug into the next well. This allows for multiple wells to be addressed without the need to recover equipment or even move the vessel back into proximity of the facility.
We are also preparing a variant of the system that interfaces with a production manifold (versus a subsea tree), enabling any well connected to that manifold to be stimulated through its production jumper. An added capability necessary for this system’s initial application allows operation in sub-ambient conditions—i.e., it maintains injection integrity when the well produces at a pressure below the water depth’s hydrostatic pressure.
Effectively, the only limitation becomes how much stimulation fluid the intervention vessel can carry and/or if the chemicals can be effectively replenished without having to leave the work site. Of course, we design and build our fluid handling system on the intervention vessel to accommodate even the biggest jobs.
WO: Considering all the thought and analysis that went into developing this novel solution, has it been successful?
Wolford: Indeed, it was, and continues to be, a successful, effective solution. To date, we’ve mobilized the system aboard two different intervention vessels and deployed it subsea four times to stimulate seven wells—with more than 9 million gallons of stimulation fluids pumped.
About the Authors
NATHAN WOLFORD is a subsea systems consultant, working with C-Innovation on their riserless well stimulation solution. Working out of Bluefin Subsea LLC, he has consulted on various projects since 2014. Previously, he was project engineer and project manager for Wild Well Control, from early 2011 to early 2014. Mr. Wolford also served as a project installation engineer for FMC Technologies from August 2007 to early 2011. He earned a BS degree in mechanical engineering from Texas A&M University in mid-2007.
KEVIN KNIGHT has been engineering manager at C-Innovation since April 2024. From June 2023 to April 2024, he was RLWI engineering manager for the company. He also was a subsea engineer at C-Innovation from mid-2016 to mid-2023. In addition, Mr. Knight was a systems engineer for FTO Services from April 2014 to July 2016. He spent eight-and-a-half years at FMC Technologies, fulfilling positions of increasing responsibility. He began his career at BWXT Pantex, working as a project specialist from February 2002 to April 2006. Mr. Knight graduated from Texas A&M University in 2001 with a BS degree in Engineering Technology and Telecommunications. He earned an MS degree in Systems & Engineering Management from Texas Tech University in 2005.
Related Articles
- First Oil: Deepwater Development conference highlights renewed interest in that sector (March 2025)
- World Oil’s Deepwater Development Conference approaches with great momentum (February 2025)
- Advancing MPD operations with integrated riser joint technology (January 2025)
- Cutting-edge choke condition monitoring: What can we do to prevent choke failure? (November 2024)
- Drilling advances: What is the Performance Twist-Off cost? (September 2024)
- First oil: Muddling through the rest of 2024 with enthusiasm for 2025 (September 2024)
- Subsea technology- Corrosion monitoring: From failure to success (February 2024)
- Applying ultra-deep LWD resistivity technology successfully in a SAGD operation (May 2019)
- Adoption of wireless intelligent completions advances (May 2019)
- Majors double down as takeaway crunch eases (April 2019)
- What’s new in well logging and formation evaluation (April 2019)
- Qualification of a 20,000-psi subsea BOP: A collaborative approach (February 2019)