The oil field gets digitalized with fast ROIs
Cratered oil prices have decimated the energy market, eliminating liquidity for many operators and placing formerly viable projects in danger of shut-in. Dreams of profit have been put on hold, as project managers scramble to find the means to keep their ventures in the black. The chief challenge, of course, is doing more with less capital and fewer people.
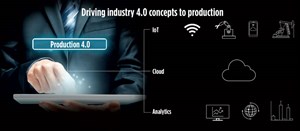
As the industry locks down capital spending, stakeholders must make the most of their resources to remain viable. However, as operators are forced to work smarter and faster, the industry has discovered it is on the cusp of new thresholds of production performance.
The answer is technology. But not technology at any price. While the industry has examples of fast and broad technology acceptance—think unconventional drilling and completion breakthroughs from last decade—the oil and gas industry is stubbornly slow to adopt new innovations.
If there ever was a time to move beyond the fear of investment, it is now. And if there ever was a time to accept breakthrough technologies, it is now. Embracing Industry 4.0 capabilities and digitalization is no longer a question of simple efficiency, it is the answer to remaining viable through this downturn and beyond. This is the only way we, as an industry, can make profitable gains that will make a difference today.
DIGITALIZATION BRINGS CERTAINTY TO ROI
By harnessing Industry-4.0 capabilities, and now by incorporating open architecture, virtually anyone can access previously unimagined thresholds of efficiency and control. Industry 4.0 comprises the Internet of Things (IoT), Cloud computing, Edge connectivity, and advanced data analytics. IoT is comprised of digitally connected physical devices that add systematic support and efficiencies through empirical data and remote controls.
Cloud computing allows these devices to network through Internet-hosted servers that store and manage data while reducing infrastructure and complexity. Edge computing then elevates this connectivity with intelligent devices that can make real-time, autonomous decisions, based on live data and historical models.
As the leading wellbore- and production-solutions company, Weatherford set a course to adopt Industry-4.0 concepts—proven in many industries, such as manufacturing, logistics and entertainment—and applied them to the production phase. Embracing digitalization is no longer a question of simple efficiency, it is the answer to remaining viable through this downturn and beyond. Weatherford calls it Production 4.0. And it represents near-perfect asset efficiency with super-fast returns and big, long-term profits.
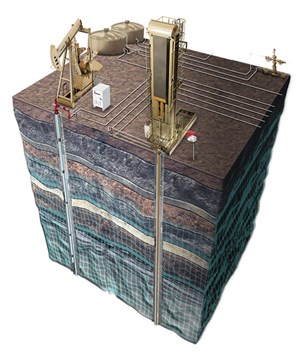
Production 4.0 solutions place a premium on fast returns for operator investments, followed by dramatic values over time, Fig. 1. In an average of just three months, operators are recouping their investment while adding incremental revenue in the millions, even during the current market downturn.
The cornerstone of these gains is the ForeSite production optimization platform. This software platform harnesses data from every corner of an asset to collectively improve the performance of a reservoir, its wells, and surface facilities. This single platform uniquely integrates physics-based models and advanced data analytics to increase equipment uptime and ultimately extend the life of an asset, Fig. 2. This secure and easy-to-maintain platform creates an entire production ecosystem to empower operators with the foresight to maximize production and reduce operating costs.
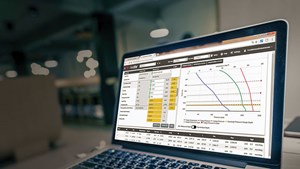
By leveraging the production-optimization benefits of ForeSite, Weatherford now presents a CAPEX-free approach, by which investors can immediately generate increased cash flow, optimize the productivity of their assets, and reduce overall expenditures, Fig. 1. Furthermore, this platform has the proven capacity to reduce the amount and severity of equipment failures, which provides even greater savings with fewer personnel requirements in the field. For the mid-term, these strategies maintain and enhance the value of an asset through digitalization solutions by establishing baseline datasets that enable pinpoint-efficient operations and exacting KPIs moving forward. These data, in turn, allow quick and profitable gains for increasing cash flow, smoothing out production curves, and reducing failures.
PROVEN: IMMEDIATE ROI’S
Colombia operator boosts production 6% in months, increases well restarts by 36% during blackouts. Production 4.0 solutions add immediate operational value. Within weeks of the phase-1 roll-out of ForeSite, a major Colombian operator managing nearly 3,000 wells increased production and efficiency gains. The Phase-1 implementation covered more than 600 wells that were identified as a subset of actively producing electrical-submersible pumps (ESPs) for further analysis. Using the ForeSite well-trend layout, each well was analyzed for its production history and operating conditions to identify uplift potential.
This discovery process yielded recommendations for minor modifications to the lift strategy in several wells, which would increase production—all Capex-free. The operator then selected a sample of those wells to test the strategy and modified each well’s ESP-motor frequency to match ForeSite recommendations. In the first weeks following the execution of this strategy, the operator realized a certified 6% incremental increase in production, with additional gains forecasted. These modifications to the lift strategy created an additional $3.25 million in incremental annual revenue.
The ForeSite platform enabled the operator to roll out their enterprise-wide digitalization strategy. Weatherford provided the entire installation, technical support, and training services, including optimization for all forms of lift, surface facilities, and pipelines. As work continued, an 8% additional increase of uncertified incremental production was reported, with total uplift recommendations for the asset expected to reach even higher production yields.
The immediate savings and benefits for this Colombian operator continued, as the country entered its annual spring rainy season. Following the ForeSite installation, this conventional-reservoir operator experienced power outages during the Covid-19 global lockdown. A multi-day deluge resulted in rolling blackouts that affected three of the fields, which included more than 1,000 ESP-lifted wells. Over a three-day rain, the operator faced nearly 850 ESP wells without power and production losses of up to 14,500 bopd.
ForeSite quickly enabled control-room operators to recognize the outage in less than one minute. Upon power restoration, one operator used ForeSite to issue a remote restart command that recovered all wells 36% faster than previous times. The immediate, Covid-19-compliant well-restart process incurred only 3 min. of downtime. As the power outages continued through day two, one operator recovered 28 wells in just 70 sec. Then, on day three, nearly 850 wells across three fields went down. However, the ForeSite platform enabled each control-room operator to recognize the failure and immediately use restart commands upon power restoration. Three control-room operators recovered 95% of the 850 wells in only 56 sec.
The ForeSite platform enabled the operator to minimize downtime, and deferred production, caused by the multi-day, rolling blackouts affecting the wells and losses that would have accumulated at the rate of 14,500 bopd. Rather than a manual restart process, which would have incurred substantially higher production losses and downtime, leading to revenue losses of up to $1.7 million at $40/bbl, the ForeSite platform enabled a fast and remotely managed process. Once again, the ForeSite investment instantly paid for itself through minimized downtime and deferred production.
PROVEN: IMMEDIATE ROI
Permian-basin operator drives $17.7-million, annual incremental value. A Fortune-500 producer with extensive assets across the U.S., and internationally, successfully implemented ForeSite to drive an enterprise-wide, production-optimization program. The mandates of the solution required accommodation for multiple forms of lift, including natural flow, rod lift, gas lift, plunger lift, and ESPs. The data-agnostic optimization platform was required to reach across multiple systems—including third-party software systems—and leverage historical data while integrating real-time feeds from the existing IoT platform, as well as other field-allocation and well-design software systems.
A ForeSite production-optimization team collaborated with the operator to assess the production strategy and data needs across more than 4,000 wells. Together, the teams agreed to a phased rollout of the ForeSite platform, which started with an 80+-well pilot to establish the KPI requirements to govern the enterprise-wide adoptions of the program. ForeSite was installed on the wells that included natural flow, reciprocating rod lift, gas lift, plunger lift, and ESPs. The system seamlessly integrated into all data-management and planning systems, and enabled the operator to manage the pilot wells by exception.
This approach identified many uplift opportunities, including recommendations to increase uptime and production in underperforming wells. This ForeSite pilot exceeded all KPIs and was immediately expanded to include nearly 1,000 wells during a Phase-1 rollout, which would ultimately be adopted enterprise-wide over the next two years.
The ForeSite platform enabled production optimization across all forms of lift, while enhancing personnel efficiency and increasing equipment uptime. Following the complete roll-out, the operator expects annualized savings of at least $17.7 million per year. These savings include $5.8 million in personnel efficiency, $6.5 million in increased equipment run-life, and an additional $5.4 million in revenue garnered from wells that with ForeSite, were transitioned more quickly from natural flow to artificial lift.
ForeSite delivered the ability to monitor performance and recognize improvement opportunities across all reservoirs, wells, surface equipment, and pipelines. This was accomplished by integrating existing data systems with real-time feeds, physics-based modeling engines, and command-and-control capabilities into a single production-optimization platform. The success of the pilot motivated the operator to institute enterprise-wide rollout of the ForeSite platform. Most importantly, the initial fast-track investment paid for itself immediately and allowed the operator to continue more proactively into the future, with even greater prospects for production gains and savings.
The brilliance of these digitalization-solution strategies is that they provide operators with immediate cash-flow results and huge, long-term investment profitability. As a global leader in production solutions, the Weatherford mandate is to reduce the total cost of ownership for an asset—whether it is 30 wells or 30,000—and deliver production solutions for assets of all sizes around the world. These strategies are already proving themselves reliable and with surprising, long-term results.
PROVEN: IMMEDIATE ROI
Autonomous lift strategy increases production 25% and reduces buy-back gas 25%. A Permian basin operator perfectly maintained optimal flowing bottomhole pressures (FBHPs) with ForeSite Edge—a next-generation controller with autonomous capabilities. Prior to adopting this technology, the asset relied on pumpers and field technicians to travel to the wellsite and perform manual pressure adjustments. This hands-on process typically required eight separate trips over a week, at a cost of more than $1,000 per well.
After installing ForeSite Edge, the operator achieved a 100% success rate for the desired FBHP setpoint, even during an issue that interrupted gas-injection rates. The operator was able to remotely adjust the FBHP range, which was maintained autonomously by the device. Altogether, this enabled significant improvements in personnel efficiency and Covid-19 operational-safety compliance.
ForeSite Edge increased production 25% per well, on average, of which 5% is attributed to autonomous control. Further, the continuous optimization decreased Opex by reducing buy-back-gas volumes 25%.
PROVEN: IMMEDIATE ROI
Edge technology reduces wellsite visits 80% for Powder River basin operator. An operator sought to improve uptime in its reciprocating-rod-lift wells that were prone to failure, each of which could only be detected by visual inspection. Each well was equipped with a variable-frequency drive (VFD) and run at high speeds. Each stroke was also prone to intermittently low pump fillage.
A Weatherford production-optimization team recommended ForeSite Edge for its high-frequency data and modelling capabilities at the wellsite—installed alongside each well’s VFD for enhanced well visibility and data availability. These devices enabled engineers to remotely monitor key performance measurements including strokes per minute (SPM), pump fillage, effective runtime, strokes per day, and inferred production. These data, along with dynamometer cards, led to optimization opportunities in each well.
Once in place, the high-frequency data and automated card-pattern matching helped engineers determine pump-fillage trends and detect cyclic gas interference, which was leading to gas pounding, increased equipment wear, and downtime. Using the system recommendations, the operator used the remote-management capabilities of ForeSite Edge to change VFD minimum SPMs, the minimum number of pump-off strokes, and SPM reduction settings. These changes increased production by an average 2%, reduced wellsite visits by 80%, reduced strokes by more than 500,000 per well/per year, and reduced failures by 15%.
By making the recommended ForeSite Edge changes, failures were reduced 15%, or 1.5 pump failures per year that cost $25,000 per failure. Remote-management capabilities increased personnel efficiency and reduced wellsite visits 80%. ForeSite Edge also revealed production-uplift opportunities that increased production 2%. Based on the success of the initial installation, the client now plans to expand the ForeSite Edge solution to additional wells across the asset.
PROVEN: SUBSTANTIAL LONG-TERM PROFITS
Middle East operator boosts revenue $156 million over three years. The Weatherford production-optimization platform enabled a Middle East operator to proactively manage failures and discover new uplift opportunities in real time for production increases over a three-year period and beyond. The operator needed to automate production monitoring, analyses, and asset-wide optimization for more than 1,500 ESP wells, with an option to accommodate other forms of lift in the future. The solution also required pattern recognition to enable predictive-failure management, as well as integrate data from six disparate systems and dozens of customized models—90% of which had underlying data-quality issues.
The Weatherford approach implemented the production-optimization platform as the sole system for its ability to manage all forms of lift.
The production-optimization platform automated production monitoring, analyses, and optimization for the 1,500+ ESP wells. This was expandable to more wells and all forms of lift, which enabled proactive failure- and opportunity-management in real time. This Capex-free solution identified improvements in production by more than 5,000 bopd, which represents a $52-million average annual increase in incremental revenues, amounting to $153 million over three years.
DRIVING CHANGE IN A CHANGING WORLD
Reactionary asset management is no longer acceptable—and much less profitable. The lost time and productivity required to isolate the cause of a well’s production problem, respond to it, and then get production moving again now represents the difference between attaining any margin at all and remaining in business. Regardless, if an investor manages 30 wells or 30,000, the chief challenge is doing more with less.
To accomplish this, operators are now laser-focused on near-term gains. Production 4.0 solutions immediately generate increased cash flow by optimizing the productivity of an asset. Expenditures are instantly reduced by alleviating the amount and severity of equipment failures, which, in turn, requires fewer personnel in the field. These solutions also deliver value in the mid-term and long term by maintaining
and enhancing the value of an asset.