The Last Barrel: Oilfield electrification, race to net-zero
Although the call for significant change and transformation of the oil and gas industry was underway prior to the Covid-19 outbreak, the drive to develop new technology to increase efficiency, lower costs and reduce GHG emissions was accelerated by the pandemic. The term “digital transformation” was loosely applied and attached to virtually any service or product touched by artificial intelligence, machine learning or the industrial internet of things. Operators and service providers were struggling to satisfy demand while reducing carbon footprint.
Since 2019, our industry has done an amazing job, developing and implementing new technologies and value-added services to reduce emissions and accelerate the drive to net-zero in a manner that also ensures an acceptable ROI. And oilfield electrification will play a critical role in the transition and help define the future of offshore and onshore oil and gas production.
Electrifying offshore platforms. Transitioning large-scale power systems on offshore platforms to run on electricity versus diesel generators enables an infrastructure powered by low-carbon energy sources, including renewable energy, says Donald Ross, president of production systems at Schlumberger. “All-electric production systems are a key part of a strategy to enable operators to meet sustainability goals using integrated subsurface, subsea and surface technologies,” Ross continued.
Schlumberger has developed a portfolio that helps minimize emissions and reduce energy consumption. It also addresses other sustainability attributes, while simultaneously driving efficiency, reliability and performance. The portfolio is divided into five subgroups: 1) addressing fugitive emissions; 2) minimizing drilling carbon footprint; 3) reducing or eliminating flaring; 4) full-field development solutions; and 5) electrification of infrastructure.
For offshore operations, electrification of infrastructure and deployment of all-electric systems are enabling the industry to deliver lower-cost, lower-carbon energy. Electrification enables sustainability benefits at multiple levels, including utilization of lower-carbon energy sources, reducing operational footprint, aligning with broader platform electrification objectives and extending reservoir drainage from a single well.
Gathering evidence. Baker Hughes is convinced that subsea electrification delivers on operators’ key concerns, when it comes to capital, operating and carbon costs. “The time is right for this technology to enter the mainstream,” says Matt Lamb, deepwater systems product manager at Baker Hughes. However, the business case is not always clear to all operators and needs to be stated robustly. No new technology can be introduced without the necessary evidence, even when the general opinion appears to have embraced it.
“So, we undertook to investigate and thoroughly analyze the potential savings available, as well as the ways in which operations could be optimized, when using electrified control system technologies instead of a conventional, electro-hydraulic approach,” Lamb continued. We selected a site that would be a credible example of a typical subsea installation and chose SNEPCO Bonga Main field, Nigeria’s first 1,000-m, deepwater development.
The study comprised a single production loop within part of Bonga Main field. It encompasses two production manifolds, and associated wells, control system and water-injection wells. The hypothetical project was assessed, as it would be for a new subsea electrified system, with real-world specifications and costings.
Capex savings. Extensive analysis showed 9% savings in subsea hardware costs at system level. Those savings come from several sources. The costs of umbilical systems were 30% lower with electric systems, control systems were 24% lower, as was testing.
Operational benefits. The study also indicates other areas in which removal of high-pressure fluid systems and rotating machine parts of the hydraulic power unit can deliver notable benefits to operators. Firstly, system availability is likely to improve, as repair demand goes down. Additionally, as hydraulic systems tend to be one of the main causes of downtime in subsea systems, the potential is there to significantly improve production availability. All of this suggests reduced opex and increased production availability.
Electrifying U.S. shale plays. To enjoy the benefits of electrification in onshore fields, an operator must build, own and operate much of the infrastructure, says Simon Palacio, business development manager, Burns & McDonnell. Building privately-owned electric grid infrastructure requires an analysis of load requirements, geographic load dispersion, supply chain and equipment lead times. It also requires load capacity available from local utilities and grid interconnection request processes.
Power system plans will assess and map the area transmission system as a starting point to develop interconnection options. It’s possible that existing utility infrastructure exists, such that electrification investment remains limited to lower-voltage distribution infrastructure. There is also the possibility that some investment in high-voltage transmission infrastructure will be required.
Cost-savings potential. While the effort may appear daunting, operators can realize cost-savings associated with removing on-site rental generators and enjoy increased electrical reliability. In the Permian basin, an economic analysis and feasibility study revealed the potential for 40% in power-related savings, with the added benefit of GHG reductions of a conversion from on-site generation to grid power. The company elected to invest in the required electrical infrastructure, which includes nine switchyards, four substations, and 400 mi of electrical distribution lines. The project showed a rate of return in less than three years, with additional benefits possible through long-term operation.
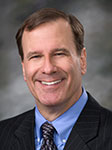
- Executive viewpoint (June 2024)
- Can an offshore drilling rig run on green methanol? (May 2024)
- De-risking carbon sequestration projects with comprehensive reservoir monitoring (March 2024)
- Solutions for decarbonizing offshore power generation (April 2024)
- Industry at a glance (December 2021)
- The last barrel (December 2021)