API leverages standards to foster innovation and adoption of 3D printing
Additive manufacturing, also referred to as 3D printing, is set to revolutionize the natural gas and oil industry by enhancing operational efficiency and innovation while helping to mitigate emissions. To tap the full potential of this rapidly expanding technology, the American Petroleum Institute (API) has developed two complementary standards on 3D printing, for polymer-based and metal components used in the industry.
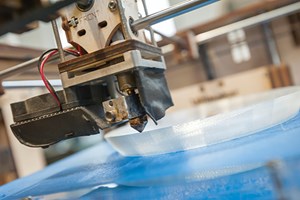
API Standard 20S, Additively Manufactured Metallic Components for Use in the Petroleum and Natural Gas Industries, and API Standard 20T, Additively Manufactured Polymer-Based Components for Use in the Petroleum and Natural Gas Industries, highlight the industry’s incorporation of new technologies and innovations to improve operations.
Focused respectively on metallic and polymer-based components, API 20S and 20T represent the baseline requirements and process controls for additive manufacturers that supply the natural gas and oil industry with components. In particular, API 20S and 20T specify requirements for qualification of the manufacturing process, production, marking and documentation of 3D printed components. The standards also provide guidance to test and document the material properties for 3D printing of polymer-based and metallic components, and they introduce three additive manufacturing specification levels that define increasing technical, quality and qualification requirements.
“These new standards reflect the industry’s focus on embracing cutting-edge technologies and innovations to meet global energy demand, while continuously striving to be cleaner, safer and more efficient,” said Anchal Liddar, senior vice president of API’s Global Industry Services. “3D printing is poised to bring significant benefits to all segments of our industry.”
A THIRD INDUSTRIAL REVOLUTION
Additive manufacturing is a process for building three-dimensional objects from a digital design, using successive layers of materials, Fig. 1. It stands in contrast to subtractive manufacturing, a traditional manufacturing process that involves carving or removing material through the machining of raw materials into a shape, followed by the assembly of several objects into a final product. Since the technology was first developed in the 1980s, as a means to rapidly prototype, it has evolved and gained further applicability in manufacturing, prompting some pundits to dub it a nascent “Third Industrial Revolution.”
Additive manufacturing has been used in a range of industries for years, including aviation, healthcare, maritime and consumer products. Today, 3D printing accounts for less than 0.1% of the $12.7 trillion global manufacturing market. However, it is estimated that the 3D printing market will be worth $32 billion by 2025 and more than $60 billion by 2030, according to a recent report, 3D Printing in Oil & Gas–Thematic Research.
The natural gas and oil industry has gradually adopted additive manufacturing in recent years, using it in drilling, for non-critical or small components, prototype development, and reverse engineering of obsolete parts that are no longer manufactured.
ConocoPhillips, for example, has been testing 3D printing for the replacement of burner plugs in original 40-year-old gas turbines on Alaska’s North Slope. Because the components are no longer manufactured, worn out burner plugs are difficult and costly to replace, often taking 30 to 60 weeks to get to the isolated region. However, by using 3D printing, it is possible to produce the components in about one week and ship them to the field location.
Royal Dutch Shell has used 3D printing for design prototyping and tooling for more than a decade, and it is increasingly deploying the technology to print spare parts in difficult-to-reach areas, such as offshore platforms in Nigeria, Fig. 2. The company cites 3D printing for cost-savings and faster lead times for end-use spare parts, including heat exchangers, impellers in pumps and polymer seal covers, which help enhance operational safety.
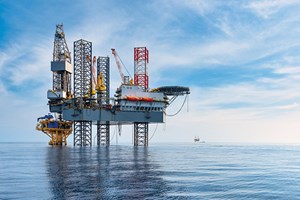
ExxonMobil, among other things, is reportedly using 3D printing for the rapid prototyping of its cMist technology, which removes water, carbon dioxide and hydrogen sulfide from natural gas to achieve safety and gas quality standards.
As the technology develops, interest in additive manufacturing is growing. A survey of European oilfield service sector executives, conducted by digital manufacturer Protolabs, showed that 82% of respondents plan to engage in 3D printing and on-demand manufacturing.
STANDARD DEVELOPMENT FOR ADDITIVE MANUFACTURING
The widening use of 3D printing has been accompanied by a number of standards-developing organizations and classification bodies—including ASTM International, the International Organization for Standardization (ISO), the American Society of Mechanical Engineers (ASME) and Norway’s DNV—releasing standards for additive manufacturing. However, from a standards perspective, API 20S and 20T are the first standards specific to 3D printing for manufacturers supplying the natural gas and oil sector with components.
Guidelines or standards for 3D printing will help ensure that components meet minimum material requirements, as well as reduce the cost of components’ qualification. Qualification is a critical process to demonstrate a component is able to meet or exceed certain manufacturing standards, such as those developed by API for the natural gas and oil industry. The lack of qualification guidance previously has also slowed down the adoption of additive manufacturing in the industry.
As the premier global standards-setting organization for the natural gas and oil industry, API, in collaboration with member companies and often with U.S. federal regulators, has developed more than 800 standards to enhance operational safety, efficiency and sustainability. Standards enhance the safety of operations, ensure quality, help keep costs down, reduce waste and minimize confusion. They help speed acceptance, bring products to market quicker, and avoid having to reinvent the wheel every time a product is manufactured.
“As the natural gas and oil industry moves to adopt 3D printing for a wider range of uses, it is critical accompanying standards meet the specific needs of an industry that often operates under challenging environments,” said Alexa Burr, vice president of Standards and Segment Services at API. “API Standards 20S and 20T will help build confidence in the technology and speed up its adoption across the industry.”
INDUSTRY BENEFITS OF UTILIZING 3D PRINTING
Additive manufacturing can provide the natural gas and oil industry with significant efficiency and cost benefits, by cutting lead times and supply chain stress. Many additive manufacturing set-ups can be deployed almost anywhere, helping to bring manufacturing of components close to the point of use. This flexibility can promote operational efficiencies in remote regions and offshore operations. It also can foster the onshoring of manufacturing and supply chain resilience across all industry segments—a vulnerability laid bare by the Covid-19 pandemic and war in Ukraine.
Operators currently stock large quantities of spare parts and components or otherwise wait for new inventory, leading to costly warehousing and downtime. The on-demand, on-site nature of additive manufacturing and the use of “digital warehouses” can help address these issues, bringing significant benefits to the natural gas and oil industry. A World Economic Forum report estimated that 3D printing of spare parts in the industry can reduce inventory levels by 2% and slash the cost of repairs, maintenance and transportation by 3%.
Compared to subtractive manufacturing, additive manufacturing optimizes the design and manufacturing process to minimize the need for machining and material removal, translating into less waste and material use. Dematerialization—or producing an end product with less material—not only saves on material costs but also helps reduce the industry’s indirect environmental footprint.
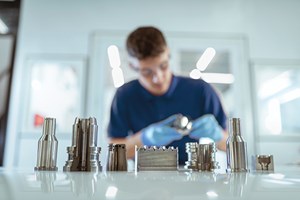
Additive manufacturing allows innovators to bring ideas to the market quickly and efficiently. Through a digital model, 3D printing provides flexibility in the design of prototypes and eases the production of custom parts that would be difficult, expensive or impossible to do with traditional manufacturing. This effectively eliminates the need for economies of scale in the production of some components.
In addition, additive manufacturing also can improve manufacturing productivity by printing complex parts in one piece, in geometries that aren’t possible in traditional manufacturing. For example, GE Aviation, a subsidiary of General Electric, has been using 3D printing to manufacture thousands of jet engine fuel nozzles for its LEAP engine. Instead of welding together 20 different pieces, the additive-manufactured jet engine fuel nozzle is composed of one piece that weighs 25% less, is five times more durable and is 30% more cost-efficient than its predecessor. Given the complexity of components used in the natural gas and oil industry, 3D printing could yield similar efficiencies while also enhancing safety and environmental protection by reducing the chance of failure of the individual parts that make up complex components.
“3D printing opens up myriad possibilities for the creative design of parts and components that couldn’t be made using traditional manufacturing, which requires welding, casting and grinding material. By allowing engineers to make digital designs without costly research and development lead times, the industry can become more efficient and innovative,” said Carlo De Bernardi, an engineer at ConocoPhillips leading API’s 20S standard group on 3D printing.
As the natural gas and oil industry continues to become cleaner and more efficient, additive manufacturing offers the potential to reduce the industry’s indirect carbon footprint.
Not only does additive manufacturing reduce the need to transport components across extended supply chains, but it also can impact the transport sector in another way as lighter components reduce fuel consumption. Meanwhile, because 3D printing requires fewer raw materials during manufacturing, or dematerialization, the industry can indirectly contribute to fewer emissions during the production of material inputs.
Therefore, the inherent efficiencies of additive manufacturing, including the need for less materials compared to traditional manufacturing, combined with reduced logistics, can drive a significant reduction in Scope 3 emissions. In doing so, 3D printing helps demonstrate the industry’s adoption of API’s Climate Action Framework, which details industry’s commitment to protect the environment by reducing greenhouse gas emissions.
Despite the promising future of 3D printing in the natural gas and oil industry, there remain a number of hurdles that must be addressed to boost confidence in the technology before it gains broader use. Natural gas and oil production takes place in challenging environments where corrosion and high temperatures and pressures are all factors that must be taken into consideration to ensure safe operations.
API 20S AND 20T PAVE THE WAY FOR BROADER ADOPTION
There are currently limits on where 3D printed components can, and should, be used, taking into account unique and challenging production environments. Therefore, further testing of additively manufactured processes and material inputs is needed to ensure that components can withstand sustained contact with hydrogen sulfide, carbon dioxide and chlorides that are part of the hydrocarbon mix, as well as perform under different pH levels, temperatures and pressures. Components’ suitability for sour and non-sour grades also needs to be demonstrated.
This will entail identifying and testing polymers, as well as metals and alloys critical to the industry, that can be produced through the latest additive manufacturing techniques in accordance with API 20S and 20T, with a focus on methods suitable for large-scale and pressure-containing parts, Fig. 3. API 20S and 20T are base documents that allow the industry to leverage these standards for various components and identify where they are best applicable. They are intended to encourage a safer, broader and faster adoption of additive manufacturing across the industry, by building greater confidence for their use in mainstream industry applications.
Ultimately, the qualification process is left to the end-user to define application requirements and develop functional specifications to meet these requirements. The specifications are provided to the original equipment manufacturer, who would then develop technical design specifications to meet the requirements, in line with appropriate manufacturing processes, material properties and quality control provisions.
It is anticipated that additive manufacturing component qualification will follow similar principles for other traditionally manufactured components used in the industry, which take into account stress-strain relationships, yield strength, ultimate tensile strength, fracture toughness, strength-temperature relationship, burst and collapse resistance and fatigue resistance of the materials and design of additive manufactured components.
API 20S and 20T represent the first steps to allow traditional components covered in API product specifications to be produced using additive manufacturing. However, it must still be determined where additively manufactured components could be added to individual product specifications.
- Aramco's upstream digital transformation helps illuminate the path toward excellence (June 2024)
- Adopting a holistic approach to cybersecurity (March 2024)
- Embracing automation: Oil and gas operators leverage new operational efficiencies (May 2024)
- The five A’s on the road to completions automation (May 2024)
- Digital’s influence on drilling and production keeps growing (March 2024)
- Taming the red zone with automation (April 2024)