Lessons from the Gulf of Mexico: Expediting an offshore platform’s decommissioning
The call to decommission offshore oil platforms has increased over the years for a variety of reasons. The primary reason is the age of the infrastructure in many locations. Since wells become less productive over time, when they reach a certain point, they are no longer economically viable and must be decommissioned, as regulated by agencies like the Bureau of Safety and Environmental Enforcement (BSEE). This is often a demanding process that can easily take up to two years to complete. However, in studying a recent Gulf of Mexico (GOM) decommissioning, one operator found ways to expedite offshore plug-and-abandonment (P&A) within a year.
There are over 12,000 active oil and gas platforms worldwide. About 387 active sites are under U.S. control, primarily divided between the North Sea and the GOM. As of 2017, 52,964 wells have been drilled in the GOM; 27,405 of these wells have been abandoned permanently, or more than half of all wells drilled. The remaining well inventories at the end of 2017 totaled 25,559. All of which underscores the imperative driving the decommissioning and dismantling of these platforms, Fig. 1. There are two main types of platforms, floating and undersea towers. The largest tower is Petronius and stands approximately 2,000 ft tall—the only taller structure on Earth is the Burj Khalifa tower (2,723 ft) in Dubai. In the GOM, the seabed is relatively shallow, so towers are the most common structures found in that location.
THE IMPERATIVES TO DISMANTLE
Dismantling an idle platform is often required as part of the licensing that a company agrees to when facilities are no longer useful for operations. For instance, regulatory organizations, such as BSEE have an “idle iron” policy in effect that states, if a platform is determined to be no longer economically viable, it needs to be dismantled within one year of the decision. Platforms are considered idle, if they have not been manned or produced resources over a five-year period. Companies that fail to meet this one-year timeframe could face fines. Worldwide, these fines will reach an estimated $104.5 billion by 2030, according to Wood Mackenzie.
The Outer Continental Shelf Lands Act (OCSLA), and its implementing regulations, establish decommissioning obligations that an operator commits to when signing an offshore lease. Under OCSLA and the Department of Interior’s implementing regulations, non-producing platforms must be removed, because they can create serious safety, environmental and navigational risks. Abandoned platforms may deteriorate, making them more susceptible to structural failure or being toppled by hurricanes and potentially damaging, neighboring active infrastructure.
Currently, the plan is to decommission and dismantle at least 23 platforms a year in the North Sea, alone (reported by Rystad Energy, May 2021). The national oil company in Brazil has said it is planning to spend $6 billion to retire 18 platforms, pipelines and other infrastructure by 2025.
HOW PLATFORMS ARE DISMANTLED
Dismantling an oil platform is a major operation, but there is generally an established process for handling such work that includes the following seven stages.
Stage 1: File the necessary paperwork. Working on a rig is dangerous, and when accidents happen, they give birth to added bureaucracy. The most common accidents involve work with cranes, accounting for half of all reported incidents, with fire incidents being the next runner-up. Most of these fire incidents involve welding, cutting torches, overheating compressors, or kitchen equipment. These types of incidents are what BSEE attempts to mitigate by making sure proper safety protocols are being followed.
In the instance of decommissioning a platform in the GOM, this would mean filing paperwork with BSEE, primarily the Application for Permit to Modify (APM), for a well P&A. Other possible forms needing submission at appropriate times include filing a Pipeline Decommissioning Application and a Platform Removal Application. In addition, other forms might be needed to address special considerations, such as using explosives to cut the jacket, especially when working in environmentally sensitive areas. BSEE should be notified two years before cessation of production, and they need to know if any abandonment is going to be temporary or permanent. BSEE also requires that all wells be plugged, and structures removed, one year after the lease terminates.
Stage 2: Perform well P&A field work. This involves capping the well and removing any recoverable equipment. For a subsea well, this would involve: 1) squeezing the current zone in the well (injecting cement slurry into a zone for pressure isolation); 2) placing the required cement plugs in the casing; and 3) putting a surface plug in the casing. This process completes capping the well. Most wells in the GOM are dry-tree, so P&A here would include cutting and removing the riser 15 ft below the mud line. Depending on water depth, this could be managed with available platform cranes. Otherwise, big barges with lift cranes would be employed during the structure removal stage.
Stage 3: Conduct facility preparation field work. This involves flushing hydrocarbons from existing equipment on the platform. This is a delicate process, since it is important to avoid spilling oil into the water.
Stage 4: Perform pipeline removal and decommissioning field work. In this stage, the pipeline is removed, and this often requires coordination between different companies, depending on who owns the equipment.
Stage 5: Oversee structure removal field work. How this is accomplished depends on the size of the platform. On smaller platforms, sometimes it is possible to leave all the equipment in place, but with larger platforms, this will need to be removed or the platform will be too heavy to lift. The most common practice is to haul off the superstructure to be sold as scrap metal. It is a common practice for third-party companies to give discounts, if you allow them to sell the structure as scrap. Additionally, there are some other methods of disposing of the structure. It could be moved to a new location and reinstalled. It could be disposed of in deep water (requires BSEE approval). Or, it could be sunk and covered on location, and possibly converted to an artificial reef.
Stage 6: Direct site clearance field work. Depending on what is to become of the superstructure, this could include any number of things. When the site clearance is completed, the site is then deemed safe for all kinds of activity in that area. For instance, if fishing boats or trawlers expect to operate in the area, it is necessary to make sure nothing is left that could snag or tear nets or cause other mishaps. This is done by sending out boats with different types of specialized nets (different from regular fishing nets) to see if anything snags and then removing any debris discovered by this process. The process continues until there is nothing left for nets to snag.
Stage 7: Submit final paperwork. In the Gulf, this means BSEE. This is the final step in a process that can easily take two years to complete.
In addition to the paperwork and fieldwork necessary for decommissioning, there is a financial component to consider, as well. Dismantling an oil platform is expensive, though much can be written off in taxes. Deepwater wells cost an average $10 million per well and about $500,000 for wells in shallower waters, like parts of the GOM. In the North Sea, the UK is forecasting paying out more than $26 billion to close its platforms in the region by 2030.
Adding to the normal financial burden is the challenge created by a push to decommission wells, all while the industry has been struggling with concerns like deflated stock prices and overproduction throughout 2020. Though oil prices have rebounded, adding the cost of decommissioning thousands of wells is an unwelcome burden. When the break-even point is crossed, the point where the cost of producing oil is more than the price being sold on the stock market is reached, banks become more hesitant about lending money. When oil prices fall too low, banks become less likely to fund high-risk ventures, such as deep-sea development.
A CASE STUDY IN EXPEDITING A DECOMMISSIONING
Most industry experts have accepted a two-year minimum to decommission a platform, considering all the factors and moving parts involved. In a recent decommissioning in the GOM, one operator managed to complete all necessary stages of P&A in 13 months. In reviewing the circumstances, could it be possible to complete such a process in under a year or even less? In this scenario, there were two connected platforms involved—a well platform and a facility platform. Timely paperwork filing aside, several other contributing factors went into this successfully expedited field abandonment, Fig. 2, as follows.
One, the operator was a smaller company and was responsible for the pipeline. The company was connected to another vendor, so when the operator knew they were no longer going to be producing, they gave them notice far in advance.
Two, there was minimal prep work needed in this instance. The project was a small platform and only concerned the wellheads and a separator.
Three, the operator was able to complete flushing the lines before contractors were called in.
Four, two lift boats were used—one doing well P&A work on the well platform while the other was doing prep work on the facility platform at the same time, helping to shave time off the project.
Five, the site stood in only 60 ft of water, which avoided the more complicated issues found in deeper waters.
Six, since the operator was a smaller company, it was able to have some flexibility regarding scheduling with contractors in terms of timelines. This proved cost-effective, as well. And seven, the GOM region has a window when the weather is calm enough to proceed with certain operations, and contractors working in the area were aware of this. These regional weather patterns help keep people motivated and force work to be focused into a certain timeframe. Based on the amount of actual labor hours needed to complete the process, weather concerns appear to be the primary factor in lengthening the project’s time to completion.
The penultimate step in the process was a site clearance survey on the blocks, which also involved filing some specific paperwork. Since commercial vessels were going to be used in the area, it was important that no debris be left in the water. Therefore, it was necessary to sweep the area with trawlers to ensure nothing was there to snag fishing nets or cause damage to any commercial ships passing over the location. The site also included some blocks left by a previous campaign, so that was also added to the site-clearance survey.
Ultimately, the field abandonment went without any notable hitches. The operator was able to submit their final paperwork (detailing the costs and verification by all parties involved) and have their bond money released just over a year from the start date, Table 1.
LESSONS LEARNED FROM AN EXPEDITED GOM DECOMMISSIONING
One of the biggest lessons learned from decommissioning these two GOM platforms was recognizing the need for flexibility, which bigger companies generally do not have. When it comes to creating timelines, the more rigid they are, the longer the project will take. The operator in this instance was free to use more flexibility (especially flexibility in handling contractors) in scheduling and tackling projects, as soon as they could be handled safely and following all existing regulations.
Another key lesson that this project taught was how important the vetting process is and the importance of trust when choosing contractors and partners. Of course, this also ties into the concept of flexibility. In the case study, the main point where flexibility was needed was regarding the pipeline removal and the structure removal. The contractor was told what needed to be done, and by allowing them to do it on their timeline it became more cost-effective for the operator. The type of work these contractors do is highly specialized, and the pool is small. Reputation is still a key factor, and it is easy to know and trust well-vetted teams who have demonstrated the ability to get the job done as needed and in a timely manner.
Identifying good contractors meant knowing they were aware of regional weather considerations and that there is a built-in time to complete work before September. After that, weather conditions begin to play a more frequent role. Weather conditions should never be far from the mind when planning on an expedited decommissioning. Lastly, completing regulatory compliance well in advance allowed timelines to be met as early as possible. It was vital to this expedited process that paperwork would not hold up the project.
EXPLORING OTHER WAYS TO EXPEDITE A DECOMMISSIONING
Another factor that can help expedite decommissioning is determining whether anything needs to be saved. If the tower is headed for onshore scrapping, this can save a lot of time. The legs can be cut, and the superstructure carefully removed and hauled away. If there is nothing worth preserving from the structure and the water is deep enough, BSEE will allow structures to be sunk to the seafloor, provided the structure will not hinder other commercial ventures in the area or be an environmental danger to local sea life.
One controversial idea that has gained traction is the conversion of old rigs into reefs. In the 1980s, this “rigs-to-reef” program was first adopted in the U.S. waters of the Gulf of Mexico. Some environmentalists surveying old platforms noticed the rich biodiversity that had grown up around them in the decades they spent in the seas. This led to the idea of converting these old rigs into artificial reefs, protective habitats that function similarly to coral reefs. When toxic chemicals can be cleaned up or disposed of in some manner, this is a way to give back to the planet and can help expedite a platform’s dismantling process. Many consider this as a possible win-win for those on both sides of environmental issues.
As of Jan. 1, 2017, 515 platforms had been converted into permanent artificial reefs in the Gulf of Mexico. Louisiana and Texas have been leading the charge in the region with 350 and 165 reefs created, respectively. These 515 platforms represent about a tenth of the total installed. Each of these sites still needs to be approved by BSEE to proceed and needs to pass certain environmental and commercial hurdles to meet that approval.
Ultimately, decommissioning an oil platform is likely to remain a costly, but necessary, component of its lifecycle. The demand for such decommissioning will likely only increase if current market conditions and temperaments remain as they are. But by reducing the amount of time needed to effect such permanent abandonments, companies can save money and lessen the detrimental effect on the environment. A single shift in thinking about how such jobs are approached could help reduce these potential headaches into more manageable components that can be expedited. Innovation and alternative ways of thinking, such as converting rigs into reefs, can also help reduce costs and waste, and even help make the planet better off in the long run.
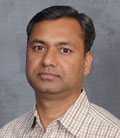
- Regional report: Guyana-Suriname: Rapid expansion of production continues (July 2024)
- Annular safety valves advance flexibility, reliability and safety in completion operations (July 2024)
- Well decommissioning: Simple solutions to complex problems (June 2024)
- Rethinking sand management for optimized production (June 2024)
- Can an offshore drilling rig run on green methanol? (May 2024)
- Custom-made blueprint for optimizing late-life assets (April 2024)