Floating ideas on safety and risk management
ABS is no stranger to the Floating Production Storage and Offloading (FPSO) market. It classed the first FPSO vessel in US waters in 1978 and continues to lead safety and innovation with new technology that supports larger, more complex FPSOs operating in ultra-deep water and in the pre-salt region of Brazil.
With more than 60% of all FPSOs in service being Classed by ABS, and over 70% of FPSOs in Brazil operating under ABS Class including 30 vessels with capacity to handle more than 100,000 barrels per day, the Houston based global provider of classification and technical advisory services to the marine and offshore industries, is committed to setting standards for safety and excellence in design and construction.
Focused on the safe and practical applications of advanced technologies and digital solutions, ABS has recently brought together leading companies in the FPSO sector to form a consortium to help address the safety challenges produced by a fleet where more than half of the FPSO vessels are over 30-years-old and a quarter are over 40-years-old.
It is a bold move that aims to advance industry best-practice to protect people and the environment bringing together industry leaders to address risks within the current and anticipated FPSO fleet. Two over-riding goals of this consortium include:
- Identifying critical risks posed to the offshore industry by an ageing global FPSO fleet.
- Determining the steps to mitigate safety and environmental risks posed by aging FPSOs.
Ageing units require more maintenance effort to maintain in Class, and maintenance needs to increase with age to reduce downtime. Across industry, it is widely accepted that increases in life extensions puts an increased burden on ageing asset maintenance issues.
The new consortium which includes Chevron, Shell, Petrobras, MODEC, and SBM Offshore, as well as the Bahamas Maritime Authority, the Republic of the Marshall Islands Registry, and the US Coast Guard 8th District, has created five joint industry projects (JIPs) aimed at using technology to tackle a range of FPSO safety issues.
The JIPs, which make up much of the work activity of the consortium, are essential to help share experience, knowledge, ideas and ways in which critical risks can be better managed from a safety, efficiency and cost perspective. Members of the consortium are already discussing how new learning can be factored in to future FPSO design, including how Class Rules can be enhanced to further provide support for tomorrow’s FPSO designers, newbuilds and operators.
This type of approach provides the opportunity for all the stakeholders in the FPSO value chain to pool their knowledge, technical expertise and their resources to deliver better safety outcomes – and deliver on a shared commitment to quality, compliance and continuous improvement.
Deep diving in to issues
Efforts of the working group will produce outcomes that will assist with the evaluation of whether equipment is still suitable for continued service and potential acceptance of life extension. For example, working groups will tackle composite material repairs for offshore structures and include aspects such as life extension of wire rope mooring systems which have been in existence for 20 years and are approaching the end of their design life.
As the FPSO fleet ages, the timely launch of the consortium is providing a forum for manufacturers and operators to come together to talk about the risks they identify that are specific to aging FPSOs, especially those risks that were not being adequately addressed, such as:
- Hot working during standard operation is challenging
- Marine and Operating groups are not aligned
- Best practices are not presently shared
- Design of FPSO units doesn’t align with actual use
- Competency of personnel
Collectively, members will all work together to determine how best to mitigate these risks and to find tangible actions that will help reduce risk posed by aging FPSOs. Discussions have started which include the prospect of a five-year engineering check, which includes a review of the overall structural integrity of an FPSO, survey and UTM reports to support decisions of surveyors and identify any areas that need to be changed. This includes loading conditions, produced water management, metocean conditions, calculated corrosion rates, residual structural and equipment strength, and cumulative fatigue damage.
Technology supporting a better analysis
It has been determined by Marine Insurance Companies and the International Maritime Organization (IMO) that 60 to 80 percent of Marine losses of life, property or damage to the environment are due to human error or a human factor.
To take equipment out of service and to examine both its external as well as internal condition is a challenging exercise. One of the JIPs has a mandate to assess the use of management software; applications of photogrammetry and 3D Lidar laser scanning; and the role of artificial intelligence in corrosion detection and analysis, particularly in terms of hull and structural integrity. FPSO Digital Twin Lifecycle approaches are critical in this area to help test and validate equipment or structures on a digital asset with that of the in-field asset to help expediate decision making and reduce non-service productive time. It can be safer, faster, and more cost effective using a digital platform and safeguards human intervention for inspection in often challenging or dangerous environments. It offers a move away from the traditional inspection methods and eliminates human-entry, as well as reduces reactive repairs by corrective action to preventive and predictive maintenance.
Last year, ABS created an AI tool that has the capability to look at images of equipment and structures and helps to evaluate the actual percentage of corrosion in that item. It is a clever innovation that can also estimate corrosion rates based on image analysis to a high degree of accuracy.
AI can be ‘trained’ and enhanced in its operation with more direct assessments on equipment and structures. In doing so it can quickly educate itself with the breadth and scope of different image assessment and corrosion rates on various items.
Making improvements to Class
ABS has developed its Rules, with a significant number of changes applicable to FPSOs, both for existing units and for new facilities. These Rule changes are intended to address many of the risks related to aging FPSOs from both a design and a maintenance perspective.
The working group are overseeing the efforts of this JIP which has resulted in more than 40 changes to the ABS Class Rules regarding FPSOs. These changes are already being assessed for implementation during this year to help reduce risks related to aging FPSOs. These changes and improvements will be shared with the launch of new publications and best practice guides regarding FPSO maintenance and inspection.
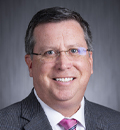
- Advancing MPD operations with integrated riser joint technology (January 2025)
- Offshore Technology: Safer by technology (January 2025)
- Digitalizing training management and delivery (December 2024)
- What's new in production: Ionic liquids (December 2024)
- OEE insurance as a well control tool (December 2024)
- Accessing wells beneath deepwater facilities (December 2024)
- Subsea technology- Corrosion monitoring: From failure to success (February 2024)
- Applying ultra-deep LWD resistivity technology successfully in a SAGD operation (May 2019)
- Adoption of wireless intelligent completions advances (May 2019)
- Majors double down as takeaway crunch eases (April 2019)
- What’s new in well logging and formation evaluation (April 2019)
- Qualification of a 20,000-psi subsea BOP: A collaborative approach (February 2019)