Subsea trees and the path to standardization
Subsea Christmas trees are central to offshore systems, where they serve as the connection between wells and the infrastructure required to bring oil and gas to the surface. Their installation requires accuracy to establish a perfect fit in difficult subsea conditions beneath thousands of meters of water—with the added complication of working with volatile materials at extreme pressures.
These components are precision-engineered for a high-pressure subsea environment. As such, subsea trees are subject to extensive safety regulations and engineering specifications. Operators have strict requirements covering the documentation, quality standards, manufacture and testing of subsea trees.
While subsea trees have traditionally been viewed as requiring bespoke engineering design, Aker Solutions adopted an innovative approach toward standardization when tendering for Equinor’s Johan Castberg project in the North Sea. Central to this approach was a robust challenge process, where Aker Solutions helped Equinor to minimize their custom requirements. As a result, the provider developed a standardized subsea tree that met Equinor’s requirements and upheld safety standards, Fig. 1.
Traditional approach. Although operating companies work in similar conditions, each organization has a unique set of standards and documentation requirements. Every project differs from other installations in terms of specific operating parameters, including well pressure and flow. As a result, subsea trees are unique components, with each project requiring a custom engineering design. Tailored solutions are expensive and energy-intensive, because they offer none of the efficiency benefits of standardization and mass production. Designing and manufacturing bespoke subsea trees also negatively impacts the industry’s carbon emissions.
There are other disadvantages to a customized approach. A unique subsea tree has no matching spare. Should a tree fail, it could take several months to manufacture a replacement leading to unwanted downtime and loss of revenue. To avoid this, operators often invest in a spare for each application, with an exorbitant capital cost. During the project phase, there is a point of no return. Changes in design or duty cannot be accommodated once manufacturing has begun. Standardization of subsea trees was not considered possible in the past. However, Aker Solutions and Equinor have challenged these accepted conventions and implemented a new strategy, with significant benefits to the industry and beyond.
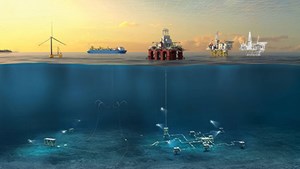
Standardized solution. A critical principle of standardization is determining which functionality to include in the design. There is a balance between keeping the design as simple as possible while still retaining all the functionality that operators could need to get the well flowing. Getting this principle wrong is the reason most standardization attempts have failed in the past. There is a temptation to include every possible mode of operation and functional requirement into the standard. The result is a part usable in any project but too expensive to manufacture. This problem is what has typically stranded historical standardization initiatives.
Standardization is difficult without common agreement about documentation requirements between operators. Without this agreement, a suitable unit may be rejected by a certain operator, because the documentation doesn’t match their internal system. This principle is fundamental when operators are sharing spare parts. Attaining this level of collaboration was a significant achievement in the standardization journey, because operating companies traditionally have been reluctant to share information at that level of detail.
Through their collaborative process with Equinor, Aker Solutions has developed a standardized vertical tree portfolio:
- 7×5 VXT on WH—7-in. vertical bore with 5-in. outlet
- 7×7 VXT on WH—7-in. vertical bore with 7-in. outlet
Each tree is fitted with a flow control module, depending on its duty—producer, gas injector or water injector. The tree remains standard, but the flow module is configurable. Standardized equipment may still be revised, using a strict management change process. This flexibility allows engineers to learn from new project installations and make adjustments that lead to continuous improvement.
Collaborative approach. The first attempt at standardization was a standalone process performed by a dedicated engineering team. However, there are many interfaces involved that made this process impractical. Aker Solutions deduced that the only way to design a standardized subsea tree was to eliminate the barriers between different disciplines in the design process. Only when all SPS-development teams worked together, could they make progress with defining the parameters for a standardized tree, including all interfaces. They used an internal interface register to help define and agree on the final design.
Besides interfaces, project cost is another major parameter requiring collaboration. Each work pack has a budget, but the impacts of one budget on another are difficult to quantify. One discipline could generate substantial project savings by overspending. However, when each team operates in isolation, that total saving may never be known. With regard to standardization, collaboration in terms of cost is critical. This is because a standardized subsea tree may be more expensive than a custom version, but the project savings from standard interfaces more than compensate for this cost.
Successful collaboration extends beyond the project engineering environment to the operating company, too. Operators are familiar with specifying bespoke trees for each project. They have a natural pushback to the idea of standardized units. Therefore, to move forward in standardizing any subsea component, engineering and operating companies must work together to overcome preconceived ideas of what may be possible.
When client representatives resist a standard subsea tree as unsuitable for their application, the project team must challenge this conclusion, to determine whether it is accurate and whether they can overcome the obstacle without changing the standard. Without this rigorous and robust challenge process, no standard can be formed, nor will it remain in place. Equinor and Aker Solutions worked together to understand these impacts and challenge the operating conventions and requirements that limited the amount of standardization achievable. Throughout this process, one specific principle was upheld—under no circumstances were safety parameters challenged, due to the severe consequences of a safety incident or regulations.
Benefits of a standardized subsea tree. Standardized trees generated immediate project benefits, due to the subsea protection system’s (SPS) size reduction. The weight of a four-slot template was reduced by up to 210 tonnes, resulting in:
- a direct cost-saving from eliminating this steel from the project.
- a CO2 saving from not manufacturing, cutting, treating, welding and painting the steel.
- a sustainable solution applicable to all future projects, too.
In terms of sustainability, when oil and gas wells come to the ends of their lives, standard components can be retrieved and—in a cost-effective way—be refurbished for use in other applications. This reuse will contribute to the circular economy and minimize waste for decades, Fig. 2.
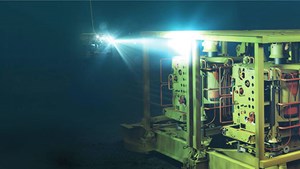
Lean teams. Aker Solutions has one team supporting almost ten installations for Equinor. They are breaking internal records for installing tube hangers and trees, due to the predictability and consistency that come from working with standard parts. Even new rig personnel can use the latest procedures and experience by previous teams to ensure a trouble-free installation. This lean approach would not have been possible without a standardized subsea tree and the associated systems and processes. Historically, project execution would have been staggered to accommodate the resource constraint. Thus, standardization is a key enabler for project optimization by making project execution quicker and lowering labor costs.
Value delivered. Offshore teams using the standardized trees and tube hangers are positive about this innovation and its impact on their operation. Aril Magen Olset (Supervisor, Offshore Services) said, “I have more than 25 years experience for offshore, installing different innovations of trees. Nothing motivates us more than smooth operations and a satisfied customer. And this is what we have achieved with this new system.”
A core benefit of standardization is the sharing of spares. A single standardized tree can act as a spare for several operators. This dramatically lowers the cost of the spare, and it allows for rapid deployment to the facility, where it is needed. One example is the tree cap that acts as a secondary barrier. Aker Solutions received a call on a Friday afternoon from an operator requiring a replacement part on the following Tuesday. It would typically be impossible to make, test and deliver this component with this short lead time. However, because they used a standardized tree, Aker could supply the cap in time from another application, with more time for manufacture and delivery. Standardization made it possible for an operating platform to minimize downtime without impacting the schedule of another project.
Another client required a gas injection tree prior to completing a producer, which was out of sync with an existing schedule. The producer tree and flow control module were already manufactured and assembled. However, removing the production flow control module and replacing it with a gas injection flow control module was a simple change. Using a standardized tree enabled the operator to change the project execution substantially without impacting the overall schedule. This saved an estimated three to six months of delay, due to standardization.
Simplified supply chain management. Having a standard tree also simplifies the associated equipment, including tube hangers. Horizontal tube hangers that connect to bespoke vertical trees may have over 150 part numbers. But there are only two part numbers for horizontal tube hangers associated with the standard tree. This simplification can generate significant savings in purchasing and supply chain management. Standard tube hanger spares also can be shared among operators in the same way as tree equipment.
The oil industry and beyond. Aker Solutions has sold over 100 standardized subsea trees into the oil and industry and beyond. These trees have been installed in the facilities of three different subsea operators, proving that the unit is truly standardized for the industry. Even though the standardized tree was designed for the oil and gas environment, studies show that it will also work in the carbon capture environment.
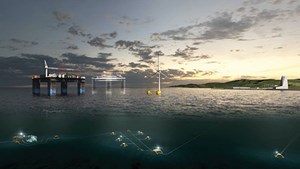
At the Northern Lights project off Norway, for example, Aker Solutions will provide its standardized subsea tree technology as part of the equipment required to inject captured CO2 into a reservoir for permanent storage. This project will contribute directly to carbon reductions that are expected to be 1.5 million metric tons per year in the first phase, starting in 2024. Over time, the subsea tree standard for CCS may be refined to create an optimum unit for that environment, which could differ from the current standard. Nevertheless, the starting point of an oil and gas subsea tree makes this refinement over time incremental rather than starting from scratch, Fig. 3.
On the human side, standardization can lead to a perception that engineering products are becoming more of a commodity, resulting in lower demand for engineers. However, experience documents that engineers released from repetitive tasks contribute to more value-adding work. There are significant benefits to be gained in many areas of engineering projects with the right level of focus, innovation, and engineering skills. Engineers seldom have time to explore these opportunities, due to the load of routine engineering tasks.
Standardization allows more freedom and creates opportunities for engineering advances. This includes developments in related industries like carbon capture. At the same time, engineers can accelerate project schedules, making more projects economically justifiable and increasing profitability for engineering companies and operators.
Next steps. Oil and gas operators and the carbon capture industry are moving toward standardization. Due to the radical nature of this change from the bespoke philosophy of several decades, it will take time to change the culture of the industry. However, we are likely to see other components follow a path similar to that of the subsea tree, as the benefits of standardization become more visible.
The new subsea trees have contributed to a higher level of standardization of control modules. Engineers are working on taking these initial steps further for control modules, structures and other subsea engineering components, using the same principles that have proved successful with the tree product. The level of standardization will differ for different parts, because some components are highly dependent on the process parameters of the well or the physical conditions, including depth and seabed conditions. Nevertheless, those functions and features that can be standardized will help to simplify future engineering designs.
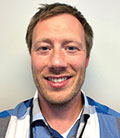
- Regional report: Guyana-Suriname: Rapid expansion of production continues (July 2024)
- Annular safety valves advance flexibility, reliability and safety in completion operations (July 2024)
- Well decommissioning: Simple solutions to complex problems (June 2024)
- Rethinking sand management for optimized production (June 2024)
- Can an offshore drilling rig run on green methanol? (May 2024)
- Custom-made blueprint for optimizing late-life assets (April 2024)